PCBs are an overlooked but vital and near ubiquitous part of electronic devices. Before the widespread deployment of printed circuit boards in the 1950s, individual electronic components were connected to each other manually using wires. This was time-consuming, error-prone and expensive. In the simplest form, a single-sided PCB, a design of conductive tracks is created on a non-conductive board by using chemical etches to remove unwanted copper. Components are then attached on the surface of the board so that the conductive tracks connect them up. The substrate provides a mechanical support for both conductive tracks and components.
As tracks on a single-layer board cannot cross each other, more complex designs are typically double-sided, while for the most complex circuits a multi-layer PCB is required. This consists of multiple layers (up to 50) of insulating substrates with conductive tracks etched onto on both sides. The substrate layers are sandwiched together with the insulating substrate stopping each of the copper layers from touching and forming an electrical connection. The connective tracks loop around each other, passing from layer to layer through conductive regions, which are formed by drilling through the insulating substrate and depositing conductive material on the drilled area to make an electrical connection through the hole. Manufacturers of electronic equipment typically outsource PCB production to third parties.
Typically, the manufacturing process limits the size of PCBs to a length of 610mm. These restrictions mean that PCBs are only used to connect electrical components that are relatively close to each other. To connect components that are further apart, for example at either end of an aircraft wing or from the rear lights of an automotive to the dashboard, individual wires still need to be used. If there are multiple wires going from one part of an aircraft wing to another (for example), the wires are usually bundled together to form a wiring harness.
IHT replaces wiring harnesses
Trackwise has developed a proprietary process termed IHT, parts of which are patented, for manufacturing unlimited length, multi-layer, flexible printed circuits. This is beginning to be adopted as a lightweight, cost-effective alternative to traditional wiring harnesses in the automotive, aerospace, medical, space, scientific and industrial markets. In the same way that conventional PCBs transformed the electronic industry in the 1950s by displacing traditional wiring harnesses in electronic devices, IHT has the potential to displace wiring harnesses outside electronic devices. Since IHT is an adaptation of a proven technology, it has the transformative potential of a new technology but with much less risk.
The key benefits of the technology for users are:
■
up to 75% weight saving;
■
improved precision with regards to which components are connected to each other;
■
deployable on a machine-intensive production line (unlike wire harnesses);
■
reduced installation time;
■
ability to be bonded either onto or into a supporting structure such as an aircraft wing;
■
Ability to integrate electronic components such as sensors and microprocessors into the PCB, changing passive interconnect into a ‘smart harness’. This potentially represents a mechanism for Trackwise to develop its own products longer term, complementing its ‘build-to-print’ service.
Exhibit 2: 26m long, multi-layer flexible printed circuit for a UAV*
|
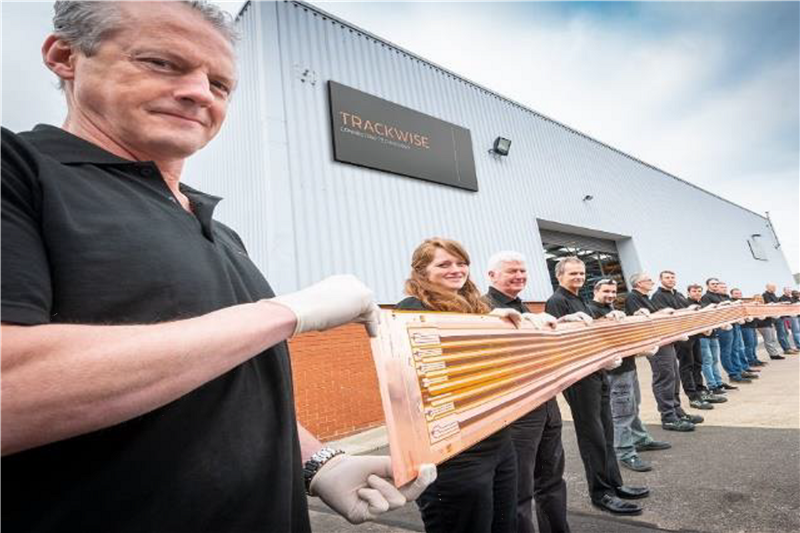
|
Source: Trackwise Designs. Note: *Unmanned aerial vehicle.
|
Adapting proven manufacturing methodology to create novel solution
Trackwise’s process is an evolution of existing techniques for manufacturing flexible printed circuits that adapts the processing steps (drilling, imaging, pressing and plating) so that previous length restrictions are removed.
■
Drilling: during high-volume manufacture of standard-length flexible circuits, a long (dozens of metres) thin strip of plastic substrate covered with copper foil passes through an automated drill. This drill is programmed to pierce a predetermined pattern of holes in a single circuit less than 610mm long, then repeat that step multiple times until the entire roll of material has been worked on. Trackwise has adapted the programme so that the drill pierces holes in the first 610mm of the circuit, then proceeds to pierce holes in the next 610mm and so on. The most complicated bit is making sure that the first 610mm section is aligned correctly to the second 610mm section and so on, and that any deviation in alignment is so small that all of the layers align correctly in the vertical plane along the whole length of the circuit when multiple layers are stacked on top of each other to form a multi-layer circuit.
■
Imaging: the roll-to-roll direct imaging process has been adapted in a similar way, so that instead of selectively exposing areas where the copper is to be retained on a single small circuit and then repeating the step many times, the machine selectively exposes the first 610mm of the circuit, then the second 610mm and so on. As with the drilling process, this requires very precise control because the minimum width track created is only 0.025mm.
■
Pressing: Trackwise has worked closely with a specialist press manufacturer to develop a continuous process that bonds the individual layers of a circuit together under raised temperature and pressure, maintaining very tight control of the process so that the horizontal layers are correctly aligned with respect to each other in the vertical plane along the entire length of a circuit dozens of metres long. At present, this press manufacturer carries out this process for Trackwise, but management intends to bring the process in-house when volumes justify this. (This expenditure is not shown in our estimates and may be financed through leasing rather than shown as a cash outflow.)
■
Plating: the new vertical continuous plating line, which has been operational since June 2019, is the first of its kind in Europe, enabling Trackwise to plate roll-to-roll flexible substrates and rigid substrates of any length.
Trackwise’s process patent incorporates the use of a continuous press to define a method for creating length unlimited flexible, multi-layer printed circuits. While the other process adaptations have not been patented, they represent a significant body of IP which is unique to Trackwise and provides a substantial barrier to entry. Trackwise has a two-year exclusivity period with regards to the adaptations worked on with the equipment supplier for the direct imaging system.
Exhibit 3: Roll-to-roll laser drill
|
Exhibit 4: Roll-to-roll plating line
|
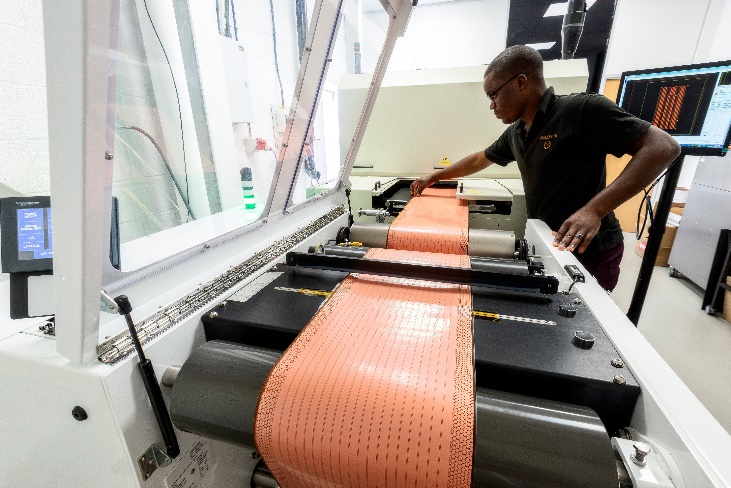
|
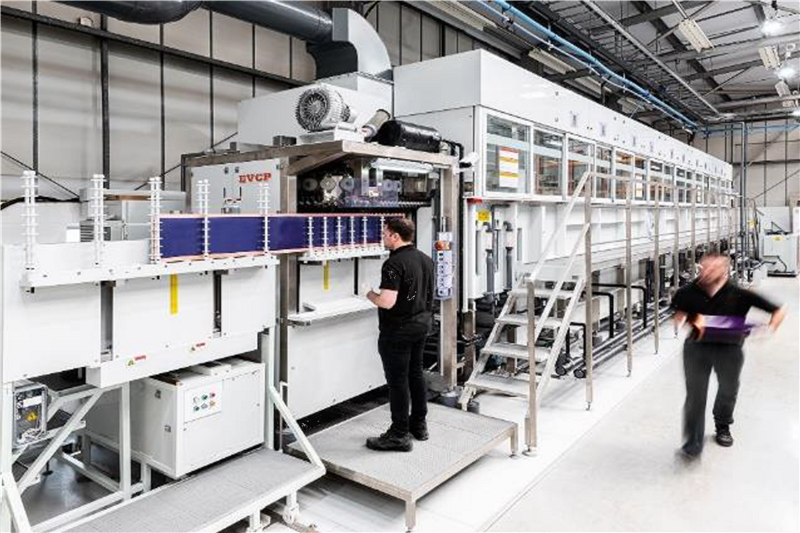
|
Source: Trackwise Designs
|
Source: Trackwise Designs
|
Exhibit 3: Roll-to-roll laser drill
|
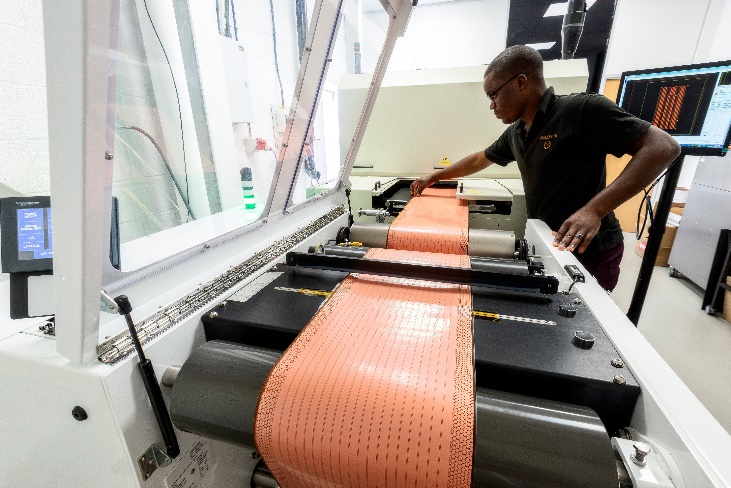
|
Source: Trackwise Designs
|
Exhibit 4: Roll-to-roll plating line
|
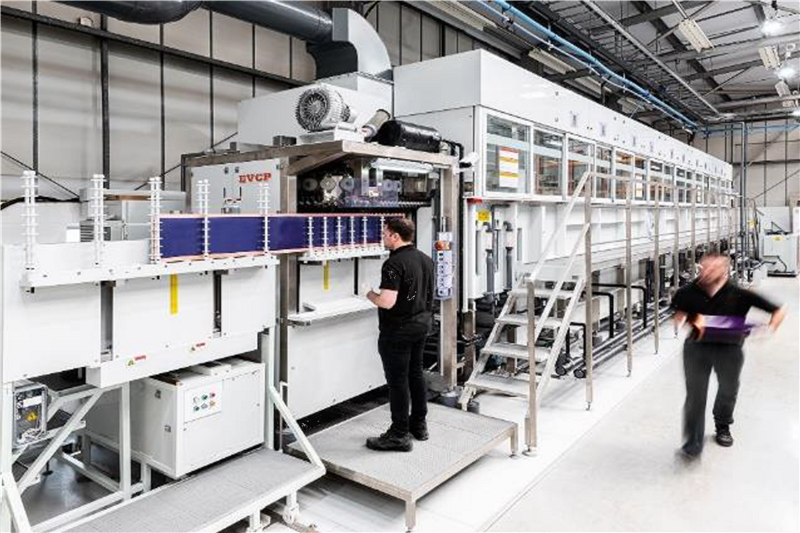
|
Source: Trackwise Designs
|
There are dozens of companies globally that can manufacture multi-layer flexible printed circuits. However, management believes that Trackwise is the only company to have extended this capability to manufacture multi-layer flexible circuits that are longer than 5m and that, while there are a few companies that can offer extremely long single- or double-sided circuits, no one else has worked out how to combine the layers to form a workable multi-layer device. While it is feasible that other companies with flexible circuit expertise would be able to modify their processes to manufacturer extremely long single- or double-layer circuits, Trackwise has the first-mover advantage. This is particularly beneficial in applications such as medical devices and aerospace where product has to go through lengthy customer and regulatory approvals. Additionally, Trackwise has patented the process required to press individual circuits together to form a multi-layer circuit.
Our independent research found that Andus Electronic in Germany claims to be able to manufacture flexible, multi-layer circuits up to 5m long, which it offers for use in tether of space exploration vehicles and in endoscopes, and US-based All Flex Flexible Circuits offers multi-layer flexible circuits in lengths up to 8 feet (2.4 metres) as a replacement for wiring harnesses. Our research did not find a company able to manufacture multi-layer flexible printed circuits of the same length as Trackwise. We believe that most companies manufacturing low volumes of flexible printed circuits will not have the ability to invest in the R&D or capital equipment required to develop a rival to IHT.
Proven product with established sales pipeline
Trackwise has been generating revenues from sales of prototype IHT circuits for the last two years. The customers are from a wide range of industries (see Exhibit 5). The most immediate opportunity is the automotive sector, where Trackwise secured its first production order in February 2020 followed by a series production order in September. Depending on how long it takes for its customers in the medical sector to gain regulatory approval for replacing wiring in catheters with IHT, Trackwise could potentially start shipping volumes of circuits for this application towards the end of 2021. Gaining FDA (US Food and Drug Administration) approval is not likely to be protracted because catheter variants with discrete wiring already have approval, so the customers only need to prove that the functionality is not changed by replacing wiring with IHT. The collaboration project with GKN Aerospace in the aerospace sector could potentially move to volume production by 2023. Although theoretically the current recession could reduce customers’ innovation budgets, there appears to have been little impact so far. We expect this situation to continue since adoption of IHT cuts the cost of manufacturing medical devices and reduces the operating costs of aircraft because of the weight it saves.
This staggered programme of customer ramp-up fits well with Trackwise’s schedule for increasing capacity. Travel restrictions related to the pandemic also delayed commissioning of the direct imaging line in Tewkesbury by around nine months to September and the final piece of equipment for volume IHT production will not be commissioned until towards the end of 2020. We explore the potential size of these three key segments (EV, medical and aerospace) in our Valuation section.
Exhibit 5: Customer programmes
Sector |
Opportunities |
Automotive |
Funded development work for UK-based electric vehicle company during FY19. First production order (£0.6m) received in February 2020 for circuits used in both low- and high-voltage circuits in battery packs. Series production agreement worth up to £38m over three years from January 2021 announced in September 2020. Discussions with other high-voltage battery module manufacturers ongoing. |
Aerospace |
AS9100 certification first received in September 2015 with the transition to the new AS9100D standard achieved in October 2017. Signed collaboration with GKN Aerospace in August 2019 for the industrialisation of an ice protection system. This is the final step before potentially moving to volume production in 2023. Collaboration agreement signed after almost two years of joint development. Study underway into use of IHT in Airbus ‘Wing of Tomorrow’. Multiple conversations with aircraft interior developers. Growing US market awareness. Second set of circuits supplied to Boeing subsidiary Aurora Flight Sciences for high-altitude pseudo-satellite (HAPS) customer following first flight in 2018. Includes a 26-metre-long, multi-layer circuit for the distribution of power and control signals across the wings. Discussions underway with four urban air mobility developers. IHT patents now secured for all main civil aerospace manufacturing locations except Brazil, which is pending. |
Medical devices and machinery |
Five cardiac catheter customers in developmental collaborations, which could potentially generate meaningful revenues from 2021 onwards depending on time required to obtain regulatory approvals (see page 15 for more details). Two of these customers are based in the US, one in Sweden. |
Space |
Collaboration with large EU spacecraft OEM for deployment in both spacecraft and in solar arrays. Qualification underway for first flight hardware. |
Industrial |
Pipeline leak detection project. |
Scientific |
CERN contract proceeding to plan. UK customer involved in nuclear fusion. |
Sector |
Automotive |
Aerospace |
Medical devices and machinery |
Space |
Industrial |
Scientific |
Opportunities |
Funded development work for UK-based electric vehicle company during FY19. First production order (£0.6m) received in February 2020 for circuits used in both low- and high-voltage circuits in battery packs. Series production agreement worth up to £38m over three years from January 2021 announced in September 2020. Discussions with other high-voltage battery module manufacturers ongoing. |
AS9100 certification first received in September 2015 with the transition to the new AS9100D standard achieved in October 2017. Signed collaboration with GKN Aerospace in August 2019 for the industrialisation of an ice protection system. This is the final step before potentially moving to volume production in 2023. Collaboration agreement signed after almost two years of joint development. Study underway into use of IHT in Airbus ‘Wing of Tomorrow’. Multiple conversations with aircraft interior developers. Growing US market awareness. Second set of circuits supplied to Boeing subsidiary Aurora Flight Sciences for high-altitude pseudo-satellite (HAPS) customer following first flight in 2018. Includes a 26-metre-long, multi-layer circuit for the distribution of power and control signals across the wings. Discussions underway with four urban air mobility developers. IHT patents now secured for all main civil aerospace manufacturing locations except Brazil, which is pending. |
Five cardiac catheter customers in developmental collaborations, which could potentially generate meaningful revenues from 2021 onwards depending on time required to obtain regulatory approvals (see page 15 for more details). Two of these customers are based in the US, one in Sweden. |
Collaboration with large EU spacecraft OEM for deployment in both spacecraft and in solar arrays. Qualification underway for first flight hardware. |
Pipeline leak detection project. |
CERN contract proceeding to plan. UK customer involved in nuclear fusion. |
Source: Trackwise Designs
Advanced PCBs for RF applications
Prior to the development of IHT, Trackwise’s Tewkesbury site focused on advanced PCBs for RF applications. Conventional printed circuit boards are not suitable for RF applications because the signal leaks from the circuit. Instead specialist substrate materials such as polytetrafluoroethylene (PTFE) are needed. There are many types of RF substrates. While they all use the same processing equipment, each requires slightly different etch times and other changes to the basic process. Unusually, Trackwise is able to manufacture RF circuits that are longer than 610mm. This means that rather than connect several PCBs together in a daisy chain, an antenna can be made from a single PCB, thus simplifying production and reducing manufacturing costs.
Established customer base
Trackwise primarily supplies antenna circuits for deployment in 4G and 5G network infrastructure. It also supplies antennae circuits for security applications, defence and aircraft radar systems, avionics and ground-penetrating radar. Trackwise’s customers are tier two or tier three suppliers to global telecommunications companies. For example, Trackwise manufactures unpopulated antennae (ie without electronic components attached) for Alpha Wireless in Ireland, a provider of innovative carrier-grade antenna solutions. These antennae are combined with other equipment by mobile network operators. Trackwise manufactures the antennae according to designs created by Alpha Wireless. Other RF customers are Kathrein Mobile Communication, one of the world’s largest antenna manufacturers, which was acquired by Ericsson in 2019, Amphenol Antenna Solutions, which is part of global interconnect group Amphenol, and the Telnet Group, a private Spanish telecoms equipment company.
In June 2020, market analysts Valuate Reports noted that the global 5G infrastructure market size was valued at US$371.4m in 2017 and projected that it would reach US$58.174bn by 2025, representing a CAGR of 95.8% between 2018 to 2025. 5G technology provides an enhanced mobile experience through reduced latency, lower cost-per-bit, and consistent and higher data rates. This enables applications such as real-time gaming, augmented reality (AR), virtual reality (VR) and autonomous vehicles, and the wider deployment of networks of smart devices, often referred to as the Internet of Things, for example networks of sensors in smart cities and smart buildings and automated industrial processes, often referred to as Industry 4.0.
Exhibit 6: Mobile phone mast with antennae
|
Exhibit 7: Antenna circuit
|

|
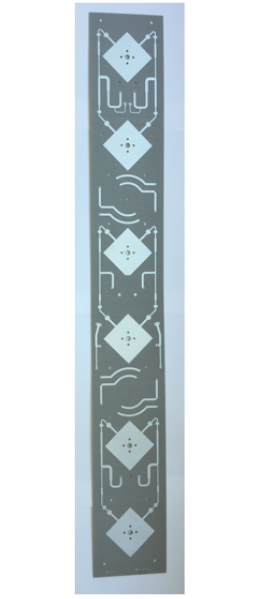
|
Source: Trackwise Designs
|
Source: Trackwise Designs
|
Exhibit 6: Mobile phone mast with antennae
|

|
Source: Trackwise Designs
|
Exhibit 7: Antenna circuit
|
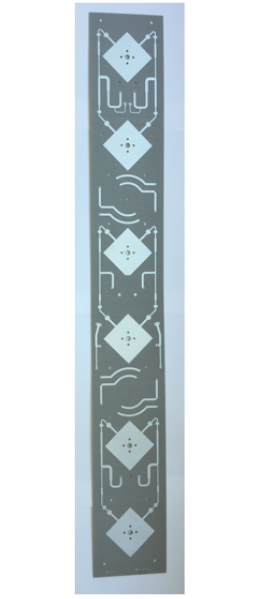
|
Source: Trackwise Designs
|
In July 2020, Gartner noted that although investment in 5G outside China was being held back by the coronavirus pandemic, global infrastructure market revenue would almost double in 2020 to reach US$8.1bn, with competition between communications service providers in all regions encouraging them to prioritise 5G projects. The report also noted that governments and regulators are directing investment towards mobile network development in the hope that this will generate economic growth to counteract the recessionary impact of the pandemic and that communications service providers are likely to increase investment in 5G networks during 2021 in order to take advantage of changed behaviours as consumers have increased their reliance on communications networks during lockdowns.
There are dozens of relatively small companies in North America and Europe that manufacture PCBs requiring specialist substrates such as those required for RF applications. These include GSPK Circuits, PW Circuits and Teledyne Labtech in the UK and Advanced Circuitry International, Cirexx and Epec Engineered Technologies in the US. Management believes that Trackwise is the only company in Europe able to manufacture long RF printed circuits. While it is feasible that other companies in Europe with RF circuit expertise would be able to modify their processes to manufacturer larger circuits, the proportion of large RF circuits has substantially reduced since Trackwise developed the technique because the frequency at which signals are transmitted has increased. This means that it is unlikely that a new market entrant would recoup its costs.
Trackwise’s RF business is focused on prototype and lower-volume PCBs, particularly those using specialist substrates. This niche is relatively unattractive to high-volume PCB manufacturers working with conventional (non-RF) substrates, most of which are based in China, because they rely on making boards in very high volumes to be economic.