2022 updated feasibility study: Smaller scale, lower risks
In January 2019, LPI published a DFS on the Maricunga project. It followed the release of a preliminary economic assessment (PEA) in early 2017 and was based on the 2018 compliant mineral resource estimate. Subsequently, the company released an updated DFS on the project in January 2022. The 2019 DFS was supported by the project’s combined lithium resources from all mining concessions (OCC and Litio 1–6). It envisaged production of 20ktpa of lithium carbonate (Li2CO3) over 22 years (year 1 to 11 from the OCC and then from Litio 1–6). The updated January 2022 study is based on the resources underpinned by OCC only and assumes production of 15.2ktpa of lithium carbonate over the 20-year life. While the reduced footprint (1,125ha for OCC vs 2,563ha for all tenements) results in a smaller scale and somewhat weaker project economics, it significantly lowers licensing and execution risks. The Litio 1–6 concessions provide extension or expansion potential, should the JV succeed in obtaining the required permits.
Lithium production: Brine evaporation versus hard rock mining
By way of background, lithium is typically produced via two main routes: saltwater brines evaporation and hard rock mining. The latter production process is broadly similar to a traditional mineral resource extraction whereby lithium bearing pegmatitic minerals, such as spodumene, petalite or lepidolite, are mined and processed into concentrate (eg SC6, or spodumene concentrate, containing 6% lithium dioxide), which is then converted into lithium carbonate or hydroxide (LiOH). In contrast, the saltwater brine is processed by water evaporation under sunlight. For that purpose, the brine, which contains lithium chloride (LiCl) as well as a variety of salts in the form of sulphites and chlorides of sodium, potassium, magnesium, boron, etc, is pumped into shallow ponds. After 12–18 months the concentration of salts and LiCl in the brine increases, salts are harvested from the ponds, while lithium is further processed into carbonate.
Exhibit 2: Lithium extraction and processing (based on Albemarle operations)
|
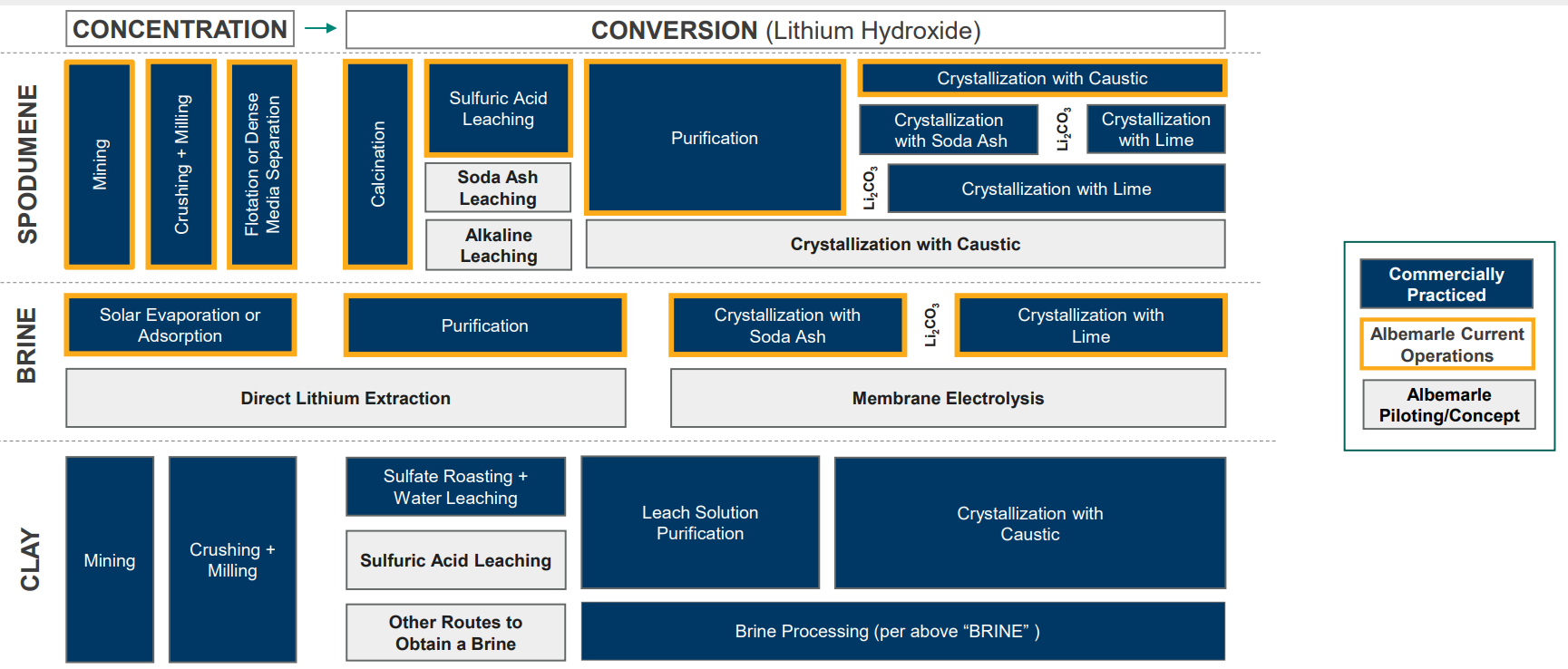
|
|
Due to the specific production routes and chemical/mineral composition, lithium from pegmatite is typically processed into hydroxide, while brines produce carbonate. In mineral processing, spodumene concentrate obtained from mining and subsequent beneficiation of ore is calcinated to convert α-spodumene into the beta phase; β-spodumene then reacts with calcium oxide to form lithium aluminate, which following leaching reacts with calcium hydroxide to form lithium hydroxide. In the schematic brine processing, sodium carbonate is added to the concentrated brine solution after the evaporation and salt removal stage, where it reacts with lithium chloride to form lithium carbonate, which can then be filtered out from the solution.
Both carbonate and hydroxide are key raw materials used in production of positive electrodes in lithium-ion batteries and can be further processed into metallic lithium. In general, hard rock mining is more energy and capital intensive and characterised by higher operating costs compared to brine processing (which is however more water intensive but overall simpler). At the same time, it is more scalable (it is not uncommon to see an integrated 40–60kpa of LCE spodumene project compared to a 15–25ktpa brine operation) and historically produced higher value-added product. However, with the recent increase in the use of lithium iron phosphate (LFP) batteries in China, carbonate now trades on par with hydroxide.
Maricunga production process: A three-stage approach
With the exception of the salt removal plant, Maricunga’s production process is similar to other saltwater salars. It is comprised of three main stages:
■
Solar evaporation ponds. This is the initial stage that takes advantage of the natural water evaporation effect and solar radiation to concentrate the brine. Evaporation ponds operate in sequence and use the brine’s natural saturation property through water evaporation and salt precipitation. When the brine reaches its saturation point it is transported to the next pond while salt is removed (harvested).
■
Salt removal plant. Concentrated brine from the evaporation ponds is fed into the salt removal plant to continue brine purification and lithium concentration by means of a series of evaporation and crystallisation steps. During this stage, calcium, boron and magnesium are removed from the brine. The salt removal plant generates more concentrated brine feed to the lithium carbonate plant, improving processing efficiency and producing higher-quality material. Importantly, it allows control of the chemical composition and stability of the feed flow to the carbonate plant and therefor maintains the quality of the product.
■
Lithium carbonate plant. This is a chemical plant that receives concentrated brine from the salt removal plant. The lithium-rich brine still contains some concentration of impurities that need to be removed through mixing with specific reagents and ion exchange. Following the elimination of contaminants, the contaminant-free brine enters the carbonation stage where it is placed in contact with soda ash to produce lithium carbonate.
Exhibit 3: Maricunga production process
|
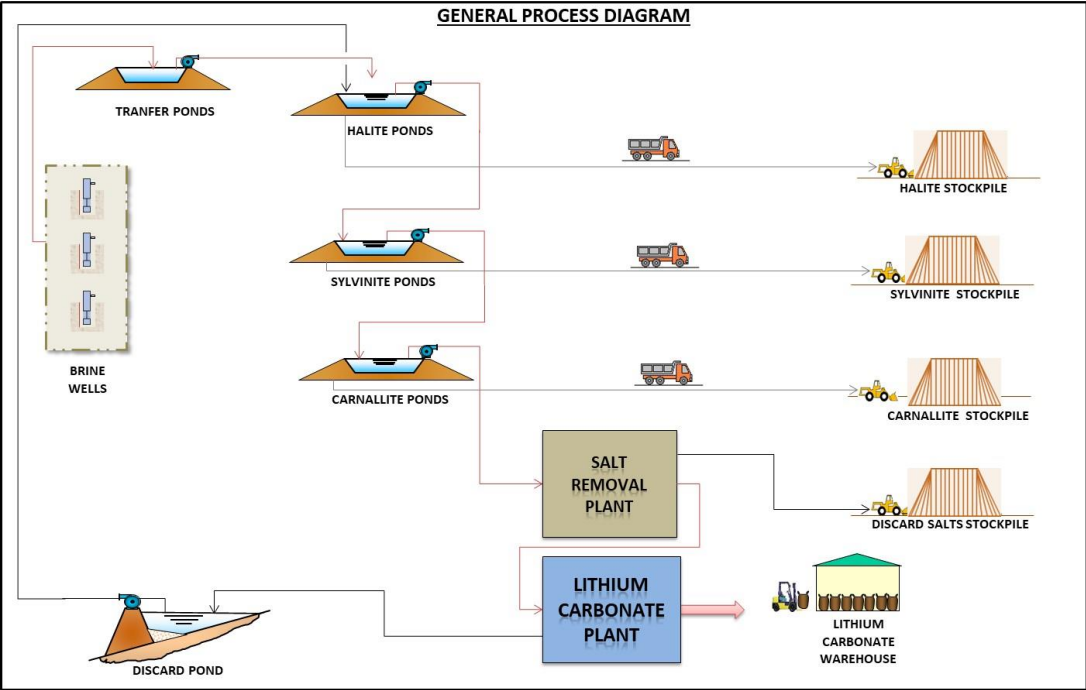
|
|
Updated reserves and resources: Estimates increased at depth
The 2022 DFS is based on the OCC mining concessions covering an area of 1,125ha, versus the 2,563ha area for the combined OCC and Litio 1–6 concessions considered in the 2019 study. Despite the smaller footprint, the project’s OCC lithium resources were significantly upgraded in the 2022 study by considering brines to a depth of 400m versus 200m in the earlier study. The project is now estimated to have a measured and indicated (M&I) resource of 358kt of contained lithium (1.9mt of lithium carbonate equivalent (LCE)) compared to 389kt of lithium (2.1mt of LCE) in the 2019 study. The project’s proven and probable reserves for OCC were upgraded to 479kt of LCE compared to 346kt of LCE before. These reserves are sufficient to sustain a 15.2ktpa LCE operation for an estimated 20-year project life. The average lithium concentration in the updated P&P reserve is 976mg/l versus 1,115mg/l for the earlier combined OCC and Litio 1–6 P&P reserve estimate, while the brine’s chemical composition is also broadly similar.
Exhibit 4: Lithium and potassium resources based on the OCC concessions (2022 DFS)
|
Measured |
Indicated |
M+I |
|
Li |
K |
Li |
K |
Li |
K |
Area, km2 |
4.5 |
6.76 |
11.25 |
Brine volume, km3 |
0.162 |
0.216 |
0.378 |
Mean grade, g/m3 |
87 |
641 |
111 |
794 |
99 |
708 |
Concentration, mg/l |
968 |
7,125 |
939 |
6,746 |
953 |
6,933 |
Resources, tonnes |
154,500 |
1,140,000 |
203,500 |
1,460,000 |
358,000 |
2,600,000 |
Exhibit 5: Brine mining reserve based on the OCC concessions (2022 DFS)
Category |
Year |
Brine volume, m m3 |
Average Li concentration, mg/l |
Contained Li, tonnes |
Contained LCE, tonnes |
Proven |
1–7 |
19 |
1,024 |
14,000 |
75,000 |
Probable |
1–8 |
13 |
1,024 |
19,000 |
102,000 |
Probable |
8–20 |
60 |
950 |
57,000 |
302,000 |
Total |
1–20 |
92 |
976 |
90,000 |
479,000 |
Total after assumed 65% recovery |
58,000 |
311,000 |
In the 2018 resource statement, Litio 1–6 had M&I resources of 184kt of lithium (979kt of LCE) defined to a depth of 200m. This resource and its extension potential to below the 200m depth level should be viewed in addition to the recently upgraded OCC estimates. The project also has significant potassium resources, which can be processed into potassium chloride (KCL). While this is currently outside of the project scope (and therefore has no value contribution), KCL production can be considered in the future and can potentially reduce operating cost as a by-product.
Exhibit 6: Schematic representation of the OCC and Litio 1–6 resources
|
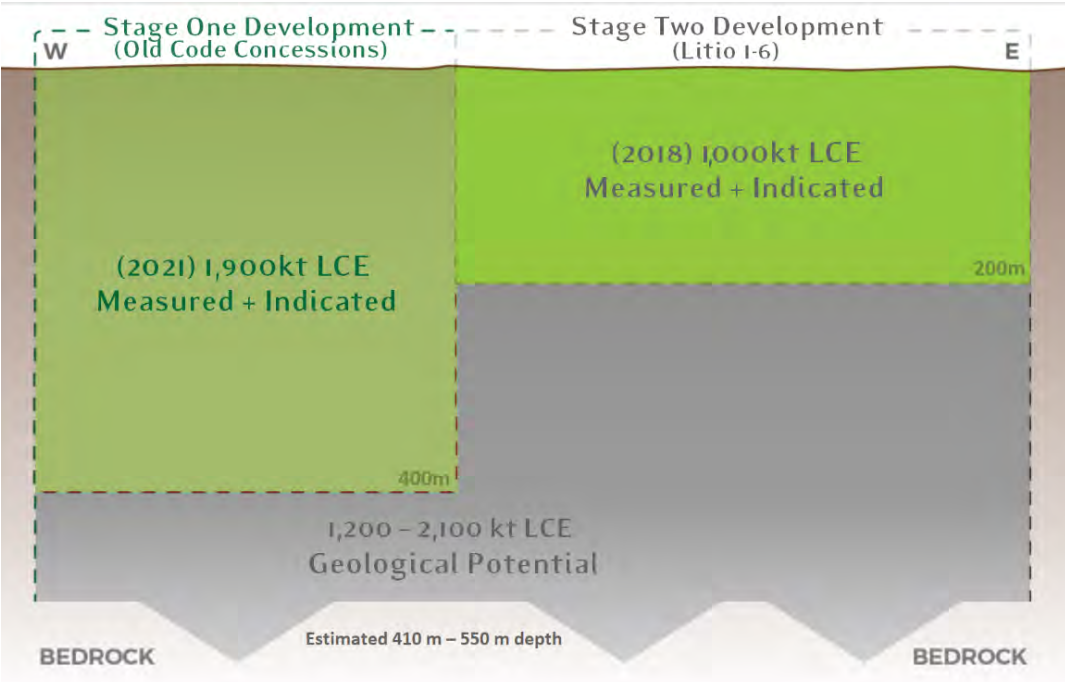
|
|
Brine quality and impurities
When it comes to the quality of the brine, lithium concentration is not the only parameter to consider. It is important to look at impurities that could have a significant detrimental effect on brine processing. For Maricunga, the main deleterious elements are magnesium (Mg), sulphate (SO4) and calcium (Ca). Its brine is characterised by a relatively high lithium concentration and low potassium content, which is favourable for processing. At the same time, the project has a high proportion of calcium in its brines. Looking at the specific values, Maricunga’s Mg/Li ratio of 6.5x is similar to Atacama, Chile’s largest and only producing salar, while its sulphate to lithium ratio of only 0.64x is the lowest among the main exploration and producing salars in Latin America (Exhibit 7). The project’s Ca/Li ratio of 12x significantly exceeds the levels reported in other salars.
The relatively high concentration of calcium and magnesium, which lowers the brine activity, as well as the levels of solar radiation at the salar are the main reasons for the introduction of an additional processing step in the form of a salt removal plant. It reduces the target concentration rate during the evaporation stage to only c 0.9% and therefore addresses the risk of the brine not reaching the required concentration of 3–4% lithium in the ponds. As a result, the salt removal plant considerably shortens the processing time. It also allows water to be recovered during processing, which is crucial as high water use during brine processing in general represents a major environmental concern, and reduces the consumption of reagents.
Exhibit 7: Brine chemical composition comparison for different salars (% weight)
|
Salar de Maricunga |
Salar de Atacama |
Hombre Muerto |
Salar de Cauchari |
Salar del Rincon |
Salar de Uyuni |
|
Chile |
Chile |
Argentina |
Argentina |
Argentina |
Bolivia |
Potassium (K) |
0.69 |
1.85 |
0.62 |
0.47 |
0.656 |
0.72 |
Lithium (Li) |
0.09 |
0.15 |
0.06 |
0.052 |
0.033 |
0.035 |
Magnesium (Mg) |
0.61 |
0.96 |
0.09 |
0.131 |
0.303 |
0.65 |
Calcium (Ca) |
1.12 |
0.03 |
0.05 |
0.034 |
0.059 |
0.046 |
Sulphate (SO4) |
0.06 |
1.65 |
0.85 |
1.62 |
1.015 |
0.85 |
Boron (B) |
0.05 |
0.06 |
0.04 |
0.076 |
0.04 |
0.02 |
Mg/Li (x) |
6.5 |
6.4 |
1.4 |
2.5 |
9.2 |
18.6 |
SO4/Li (x) |
0.6 |
11.0 |
13.8 |
31.2 |
30.8 |
24.3 |
Ca/Li (x) |
12.0 |
0.2 |
0.9 |
0.7 |
1.8 |
1.3 |
Source: LPI, company data
Exhibit 8: Lithium content in brines comparison, mg/l
|
Salar de Atacama |
Salar de Maricunga |
Salar de Olaroz |
Salar de Hombre Muerto |
Salar de Cauchari |
Lithium |
1,840 |
1,122 |
690 |
740 |
590 |
Source: LPI, industry sources
The chemical composition of the brine is broadly similar for the 2022 and 2019 feasibility studies, which cover OCC only and the combined OCC and Litio 1–6 resources respectively. Of note is a slightly lower calcium content in the 2022 DFS.
Exhibit 9: 2022 and 2019 BFS average brine composition analysis
|
Li, g/l |
Mg, g/l |
Ca, g/l |
SO4, g/l |
B, g/l |
Mg/Li |
Ca/Li |
2022 BFS |
1.1 |
7.3 |
12.9 |
0.7 |
0.6 |
6.5 |
11.5 |
2019 BFS |
1.1 |
7.3 |
13.5 |
0.7 |
0.6 |
6.6 |
12.0 |
The 2022 DFS estimates the project’s total capital cost at US$626m for 15.2ktpa, including the direct cost of US$420m and US$63m in contingencies. The main capex items are the evaporation ponds (US$90m), the salt removal plant (US$110m) and general services (US$84m). We note that the cost of the carbonate plant represents less than 10% of the overall capex. The total capital expenditure for the 15.2ktpa operation of US$626m compares to the previously estimated capital cost of US$563m for the 20ktpa operation in the 2019 DFS. The main differences are the higher cost of the salt removal plant (the cost of mechanical equipment more than doubled to US$73m) and significantly higher indirect costs (no indirect cost breakdown was provided in the 2019 BFS). The 2022 DFS is one of the most recent studies for a lithium project in Latin America and therefore includes up-to-date cost estimates that reflect COVID-19 effects. The increased cost of the salt removal plant is also due to the additional test work undertaken by the company in 2021.
In terms of operating costs, the 2022 BFS estimates total opex at US$3,864/t of carbonate, which is similar to the 2019 DFS figure. The main cost components are chemicals and reagents (28% of total operating cost), and energy (30%). The project is expected to require both electrical and diesel power, with the latter used to generate steam for the salt removal plant and it represents a significant proportion of total costs. Given the high solar radiation rates at the salar there is a potential to replace diesel with solar energy. This could significantly reduce opex. We provide opex and capex breakdowns for the 2022 and 2019 studies in Exhibit 10. We note that opex excludes royalties that are discussed in the valuation section.
Exhibit 10: Maricunga’s opex and capex breakdown for 2019 and 2022 DFS
Opex breakdown, US$/t LCE |
2022 |
2019 |
|
Capex breakdown, US$m |
2022 |
2019 |
Chemical reactives and reagents |
1,099 |
1,040 |
|
Brine extraction wells |
33.2 |
39.4 |
Salt removal |
266 |
486 |
|
Evaporation ponds |
89.9 |
115.3 |
Energy – electrical |
342 |
370 |
|
Salt removal plant |
110.3 |
66.4 |
Energy – thermal |
821 |
658 |
|
Lithium carbonate plant |
55.8 |
71.6 |
Labour |
518 |
458 |
|
General services |
84.0 |
103.3 |
Transport |
181 |
237 |
|
Infrastructure |
45.8 |
60.0 |
Maintenance and other |
491 |
400 |
|
Total direct cost |
419.0 |
456.1 |
Direct cash cost |
3,718 |
3,718 |
|
Indirect cost |
144.8 |
44.8 |
G&A |
146 |
123 |
|
Contingencies |
62.6 |
62.6 |
Total cash cost |
3,864 |
3,841 |
|
Total capital expenditure |
626.4 |
563.5 |
The Maricunga’s opex is broadly in line with the similar carbonate projects in Argentina and Mexico (Exhibit 11). However, its capital intensity is higher for both the 15.2ktpa and 20ktpa operations. This is especially so for the smaller-scale project whose lower capacity and higher capex compared to the 2019 DFS negatively affects the capital intensity. At the same time, we understand it includes the actual EPC proposals from the EPC bidding process and therefore represents an up-to-date realistic estimate. For the 2019 DFS, the project’s capex and capital intensity are relatively high mainly due to the inclusion of the salt removal plant. We also note that some of the technical studies on the comparable projects exclude owners’ costs and have a deferred capex component. While we have tried to adjust the numbers, there may still be discrepancies.
Exhibit 11: Opex and capex comparison for the selected lithium projects
Company |
Project |
Country |
Study |
Date |
Product |
Production, LCE t |
LoM, years |
Opex, US$/t |
Capital intensity, US$/t |
LPI |
Maricunga |
Chile |
Updated DFS |
Jan-22 |
Carbonate |
15,250 |
20 |
3,864 |
41,075 |
LPI |
Maricunga |
Chile |
DFS |
Jan-19 |
Carbonate |
20,000 |
20 |
3,772 |
28,175 |
Neo Lithium |
3Q |
Argentina |
FS |
Nov-21 |
Carbonate |
20,000 |
50 |
2,953 |
18,528 |
Allkem (Galaxy/Orocobre) |
Sal de Vida |
Argentina |
BFS |
Jun-18 |
Carbonate |
25,000 |
40 |
3,144 |
18,960 |
Bacanora/Ganfeng |
Sonora - Stage 1 |
Mexico |
FS |
Jan-18 |
Carbonate |
17,500 |
4 |
4,039 |
24,000 |
Sonora - Stage 2 |
Mexico |
|
|
Carbonate |
35,000 |
15 |
3,893 |
10,857 |
Sonora - Stage 1&2 |
Mexico |
|
|
Carbonate |
31,316 |
19 |
3,924 |
25,546 |
LAC (Millennial) |
Pastos Grandes |
Argentina |
FS |
Jul-19 |
Carbonate |
24,000 |
40 |
3,388 |
21,417 |
LAC (49%)/Ganfeng (51%) |
Cauchari-Olaroz |
Argentina |
FS |
Sep-20 |
Carbonate |
40,000 |
40 |
3,579 |
14,118 |
Lake Resources |
Kachi |
Argentina |
PFS |
Apr-20 |
Carbonate |
25,500 |
25 |
4,178 |
21,333 |
Liontown |
Kathleen Valley |
Australia |
Scoping study |
Nov-21 |
Hydroxide |
86,000 |
23 |
5,864 |
23,256 |
Piedmont Lithium |
Carolina |
US |
BFS |
Dec-21 |
Hydroxide |
30,000 |
11 |
3,657 |
32,933 |
Licensing and permitting status
As mentioned above, the Maricunga project consists of the OCC and Litio 1–6 mining concessions. The OCC were formed according to the 1932 Chilean Mining Code and as such, according to the company, they do not require a special licence from the Chilean government to produce lithium. The OCC (essentially two main concessions that cover an area of 1,125ha) underpin the first stage of the Maricunga project (15.2ktpa). The 1983 exploitation concessions (Litio 1–6) do not allow exploitation of lithium without a CEOL but do permit the exploration. However, historically there has been no clear and transparent process for awarding the CEOL. Under the current legislation, without the CEOL, lithium exploitation can only be undertaken by the state, state-owned companies or under administrative concessions. We understand that the JV remains in communication with Codelco, which owns adjacent properties in the salar and holds a CEOL for the area, but these discussions have not yet yielded any results.
Exhibit 12: Maricunga JV concessions map
|
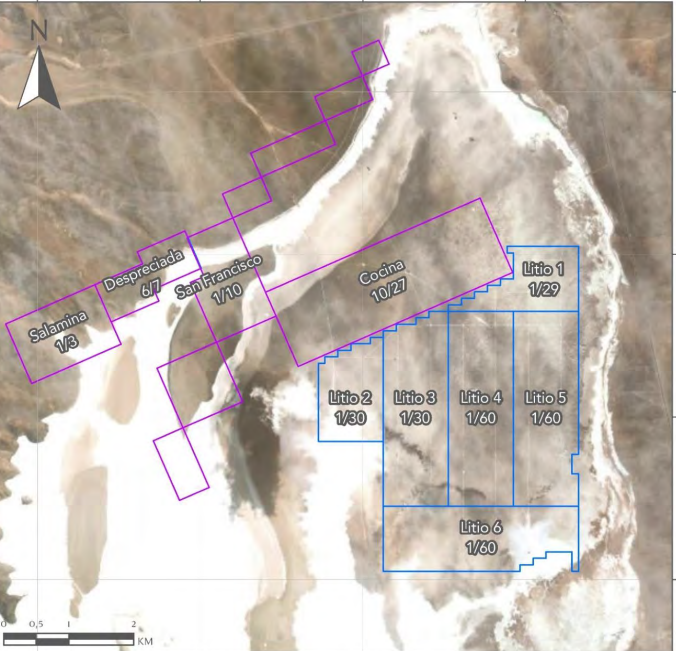
|
|
At present, the only lithium producing salar in Chile is Salar de Atacama. Both SQM and Albemarle, the world’s largest producers of lithium compounds roughly accounting for c 20% of the market each, operate in this salar. The exploitation rights in the Atacama Salar are held by the Chilean Economic Development Agency (CORFO) and are leased to SQM and Albemarle for a limited period of time. In addition to regular lease payments and other financial conditions, both SQM and Albemarle are required to pay a certain percentage of the lithium sales price to CORFO. According to SQM, these payments are incremental and at carbonate and hydroxide prices above $10,000/t and $12,000/t they could reach 40% of the price. We discuss royalty rates and other potential payments for the project later in the report, but note here that the BFS assumes Maricunga will be subject to a standard Chilean mining tax regime. The main reason for this is that the JV owns the mining concessions for the project and will therefore not be required to make lease payments to the state.
In 2019, the JV was a awarded a key operating licence by the Chilean Nuclear Energy Commission (CChEN) to produce, market and export lithium products from Salar de Maricunga. This permit is limited to the OCC concessions and allows production of 88,885 tonnes of lithium (c 473kt of LCE) over 30 years. It therefore covers the first stage of the project.
In 2020, the project received an environmental approval (EIA, the environmental impact assessment), which considered the construction and operation of a 58ktpa KCL plant (not included in the DFS) and a 20ktpa lithium carbonate plant over a period of 20 years. The JV also secured the water supply for the project through a long-term lease agreement, which was approved by the environmental agency.