Company description: Unique green cutting fuel
MagneGas has developed a patented technology for plasma arc gasification of hydrocarbon waste. The technology is used to convert butanol produced from corn into its second generation innovative cutting fuel called MagneGas2. MagneGas2 is sold into the metal working market as a safer, more efficient and cost-effective replacement for acetylene. The company also sells a variant of the gasification technology for sterilising bio-contaminated liquid waste such as pig manure or water draining from landfill so that it can be sold for use as a fertiliser or irrigation purposes rather than incurring a cost on disposal. The gasification units may also be used to convert many types of hydrocarbon-based waste into syngas or biodiesel, both of which can be used as substitute fuels.
MagneGas was founded in 2007. It is headquartered in Tampa, Florida and currently employs almost 80 people. In order to accelerate adoption of MagneGas2 and achieve economies of scale, management has recently acquired several small distributors of metal cutting gases and ancillary equipment in the Greater California and Greater Texas regions, while maintaining a network of distributors elsewhere in the US. Management’s intention is to scale up sales of cutting gases and complementary products in the US and Europe so that the resultant profits can be used to help finance R&D on the gasification technology.
Press releases from MagneGas note that customers include a global automotive manufacturing company based in the mid-West US who uses MagneGas2 at two of its sites; a heavy equipment rental company which uses MagneGas2 to repair vehicles; the New York City Department of Transportation; one of the largest recycling and waste disposal companies in the US which uses MagneGas2 in the maintenance and repair of its fleet at six locations; Pinellas County Fire Department in Florida; contractors working on NASA’s Kennedy Space Centre; major international bridge builder, Condotte; and a US army contractor for official use on a US army base for fire-rescue needs.
MagneGas2 – an alternative to acetylene
Exhibit 1: MagneGas2 vs conventional metal cutting gases
Property |
Notes |
Efficiency |
Independent tests conducted by the Edison Welding Institute in the US confirm that it cuts 38% faster than acetylene or propane and 44% faster than propane. As there is less slag in the cut edges, metal parts can be welded together without needing an extensive clean-up. Together with faster cutting speed, this improves the efficiency of metal assembly operations by at least 50%. Additionally, the amount of oxygen required is reduced by 34% compared with acetylene and 31% compared with propane. |
Safety |
Acetylene is a highly unstable, reactive gas which is prone to explosion. This makes the welding industry the second most dangerous industry group in the US. It is often contaminated with traces of arsine and phosphine gases from the manufacturing process, both of which are highly toxic. MagneGas2 is inherently less explosive, dissipates quickly if there is a leak because it is lighter than air and is not toxic. |
Production process - environment |
Acetylene production requires substantial volumes of water, while production of MagneGas2 through gasification of waste does not. Management estimates that 3bn litres of water would be saved each year if the metal cutting industry switched from acetylene to MagneGas2. |
Production process - safety |
Acetylene is manufactured by reacting calcium carbide with water. Calcium carbide is highly toxic and potentially explosive. The by-product formed during the manufacture of acetylene, calcium hydroxide (slaked lime), is harmful to humans if they inhale it or touch it. |
Footprint |
The gasification technology occupies c 10% of the footprint of conventional acetylene production equipment. This makes it easier to find room to co-locate the equipment on a site such as an automotive manufacturing facility that consumed large quantities of cutting gas. |
Property |
Efficiency |
Safety |
Production process - environment |
Production process - safety |
Footprint |
Notes |
Independent tests conducted by the Edison Welding Institute in the US confirm that it cuts 38% faster than acetylene or propane and 44% faster than propane. As there is less slag in the cut edges, metal parts can be welded together without needing an extensive clean-up. Together with faster cutting speed, this improves the efficiency of metal assembly operations by at least 50%. Additionally, the amount of oxygen required is reduced by 34% compared with acetylene and 31% compared with propane. |
Acetylene is a highly unstable, reactive gas which is prone to explosion. This makes the welding industry the second most dangerous industry group in the US. It is often contaminated with traces of arsine and phosphine gases from the manufacturing process, both of which are highly toxic. MagneGas2 is inherently less explosive, dissipates quickly if there is a leak because it is lighter than air and is not toxic. |
Acetylene production requires substantial volumes of water, while production of MagneGas2 through gasification of waste does not. Management estimates that 3bn litres of water would be saved each year if the metal cutting industry switched from acetylene to MagneGas2. |
Acetylene is manufactured by reacting calcium carbide with water. Calcium carbide is highly toxic and potentially explosive. The by-product formed during the manufacture of acetylene, calcium hydroxide (slaked lime), is harmful to humans if they inhale it or touch it. |
The gasification technology occupies c 10% of the footprint of conventional acetylene production equipment. This makes it easier to find room to co-locate the equipment on a site such as an automotive manufacturing facility that consumed large quantities of cutting gas. |
Source: Edison Investment Research
The company focused initially on the development of plasma gasification equipment to sterilise bio-contaminated liquid waste, but in the process it discovered that the synthetic gas produced as a by-product of the process was a better metal cutting gas than acetylene. It carried out further development on the process to optimise the properties of the syngas and reduce the cost of production. Exhibit 1 compares the properties of the resultant fuel, MagneGas2, with acetylene. Importantly, metal that has been cut with MagneGas2 behaves under stress in the same way as metal cut using acetylene. This was confirmed during independent tests by Certified Testing Laboratories in Florida. As MagneGas2 has similar properties to acetylene it is easy for users to switch gas type without extensive training. MagneGas2 is produced from a renewable feedstock. Since May 2017 it has been produced from butanol derived from corn. The renewable aspect does not appear to be a significant factor in purchasing decisions in the US, but it may be more significant as MagneGas begins to address the European market.
Competitive position – MagneGas2 a unique green cutting fuel
MagneGas2 is not the only fuel which is presented as offering superior cutting characteristics to acetylene. The international provider of industrial gases, Praxair sells StarFlame 3 which like MagneGas2, burns at a hotter temperature than acetylene and gives cutting speeds that are 15-50 times faster than acetylene. Like MagneGas2 there is less clean-up required after welding, further improving workshop efficiency. StarFlame is a propane variant with an additive from Chemtane Energy. Baker’s Gas and Welding Supplies in the Detroit area is a smaller player that offers a propane with an additive that produces a hotter flame than acetylene and thus cuts faster.
These alternatives to acetylene are based on propane, which is a non-renewable energy source while MagneGas2 is made from butanol obtained from maize. Management believes that this makes MagneGas2 the only renewable cutting fuel currently available. Our desk research identified Sradco, a Missouri-based engineering consultancy, who has developed a three-stage gasification system that produces acetylene from hydrocarbon waste but this does not appear to be in commercial use. Colorado-based Petrogen has developed cutting torch systems that run on gasoline, diesel and kerosene (paraffin, so could potentially be used with bio-diesel produced for other applications).
In reality the competition is from established suppliers of traditional cutting gases: acetylene and propane, which. compete primarily on price. Management currently offers MagneGas2 at a similar price to conventional cutting gases, with the enhanced safety and efficiency benefits providing a differentiator. Improvements in yield from the next generation gas production equipment currently under development (see below), should enable management to undercut the price of conventional cutting gases.
We note that as MagneGas2 fuel represents only 3-5% of sales made by its welding supply operations, these will provide a contribution towards funding the development of the sterilisation and gasification equipment regardless of the competitive position of MagneGas2. However, organic growth within these operations is dependent on securing MagneGas2 sales.
Gasification technique for making MagneGas2
Exhibit 2 Composition of MagneGas2
Component |
% by volume |
Hydrogen |
45-55 |
Carbon monoxide |
15-19 |
Acetylene |
13-17 |
Ethylene |
7-10 |
Methane |
4-7 |
Propylene |
1 |
Carbon dioxide |
0-1 |
The core technology was originally developed by the current CEO’s father, Dr Ruggero Santilli, for use in rural waste-to-energy applications. A wide range of liquid wastes containing hydrocarbons are passed through a plasma arc where a very strong electric field sterilises the bio-contaminants in the waste without adding chemical disinfectants. In the process, the waste releases a mixture of gases that burn without the emission of pollutants such as nitrogen dioxide. MagneGas is not unique in offering a plasma gasification technology, but it is unusual because its patented system enables fluid to pass efficiently through a submerged plasma arc. (We note that several of the patents expire in 2018, though others referring to the plasma arc extend to 2029 and 2030.) In sterilisation mode, the waste is passed through the arc the minimum number of times required to deactivate the bio-contaminants. In gasification mode, the feedstock is passed through the arc multiple times to achieve the highest possible gasification rate. The exact composition of the resultant gas depends on the initial waste stream. MagneGas2 is produced from butanol. Its composition is shown in Exhibit 2.
Exhibit 3: Plasma gasification process
|
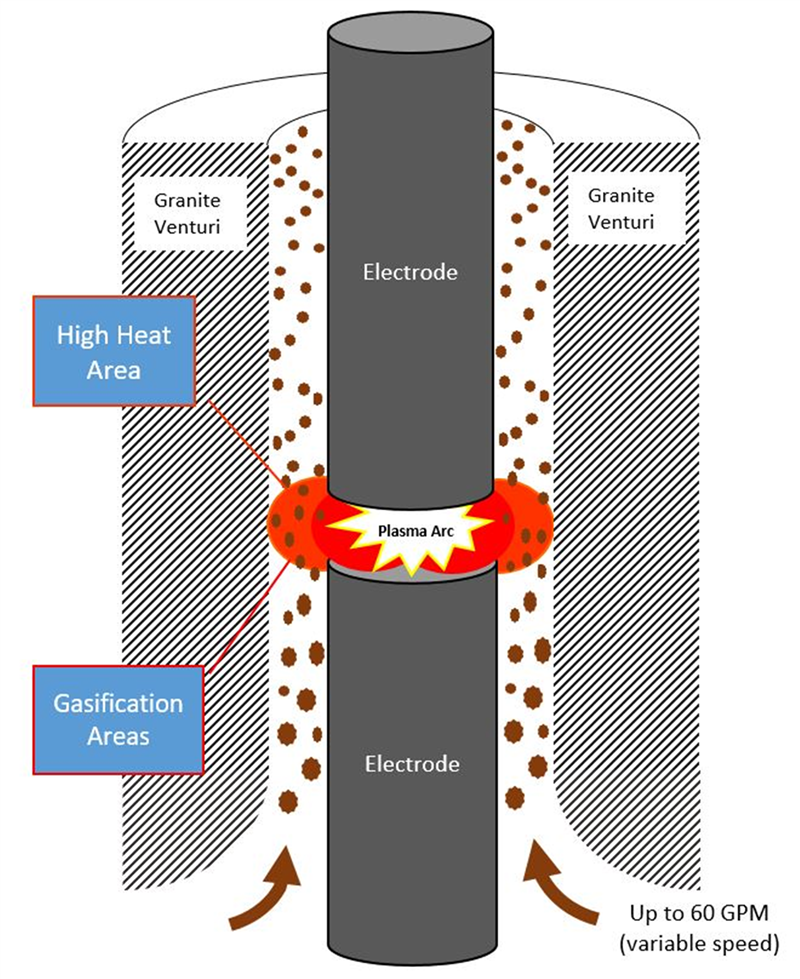
|
|
Fourth generation gasification unit under development
In October 2017, MagneGas announced that it had completed designing a prototype fourth-generation reactor after four years of work. In this updated design, a much larger area is exposed to the plasma arc. It is expected to extract around 90% of the useful gas in the first pass through the plasma arc, so that the feedstock only needs to pass through the system once or twice rather than the six to eight times in the current iteration. Simulations predict that this will reduce the amount of power required per cubic metre by 75% and increase the gas production rate for the same amount of power by at least five times. This would reduce total production costs by at least 50%, making MagneGas2 significantly more cost effective to produce than acetylene and roughly on a par with the cost of propane. The resultant price advantage should improve profits and give MagneGas an immediate ability to take significant market share in the global cutting fuel market.
Importantly, the next-generation technology will also enable the technology to be used to convert solid material such as waste plastic, bio-mass, wood chips and coal to a useful gas, opening many new feedstock opportunities. Management hopes to have a working small-scale model by the end of FY18 and a full-scale test unit by the end of FY19.
Using the gasification technology for sterilising liquid waste
The same patented technology is used as for gasification. However, in this mode liquid waste such as sewage or leachate from landfill is passed through the plasma arc the minimum number of times needed to kill any bacteria or other pathogens including E. coli and faecal coliforms. It also breaks down any pharmaceutical residue such as hormones in the waste. The technique may potentially be effective in breaking down toxic polychlorinated biphenyls which were widely used as an additive in electric transformer oils until they were banned. The process meets US Environmental Protection Agency standards for converting the liquid waste from a class B material to a safer class A waste. In one day a single stationary plasma arc flow refinery can sterilise 363k litres of sewage containing 0.8% total suspended solids. The process can be used on agricultural, municipal and industrial wastes to make them suitable for use as irrigation water or fertiliser, both of which have monetary value. For example, it costs €80/tonne to dispose of untreated sewage in landfill, but the treated product may be sold for €20/tonne as the process has little impact on the nutritional content of treated material used as fertiliser. Modest amounts of useful gas are given off as a by-product, which helps off-set the cost of sterilisation. MagneGas has also developed a smaller unit which can be mounted on a pick-up truck and shared by several farms in the same neighbourhood. The production cycle for the equipment is typically six to nine months.
Using the gasification technology in waste-to-energy projects
Since the fourth generation technology will be able to process a range of pulverised waste materials, once commercialised it may be deployed in Europe in waste-to-energy plants that process waste collected locally and produce heat and electric power for local consumption. As discussed in our PowerHouse Energy note, gasification is an attractive alternative to incineration as the extremely high temperature process breaks down toxic dioxins and furans, there is no ash to dispose of and any inorganic materials form a glassy slag which can be used as an aggregate for road-building, subject to the appropriate permits. The waste-to-energy conversion efficiency is not comparable with conventional turbines, but this is not a barrier to deployment in this application, as the waste would incur fees of €80/tonne or more if it was sent to landfill, so operators of waste-to-energy plants are able to charge for destroying the waste, in effect subsidising energy production.
Using the gasification technology for co-combustion
Since MagneGas2 burns at such a high temperature it can potentially be burnt together with coal to reduce toxic emissions from the coal as improving energy generation efficiency. Development of this application has been suspended as the use of coal in power stations is being phased out in favour of natural gas.
Gasification for sterilisation
Our competitive review indicates that Coaltec Energy is the only other company currently manufacturing gasification equipment for the sterilisation of leachates and manure. It has developed a system for producing a fertiliser material from cow manure. This can process up to 200 tonnes of raw manure each day. Coaltec appears to be at a similar stage to MagneGas, in that it is working on projects to prove the technology.
Gasification for waste-to-energy projects
We note that there are dozens of companies globally developing waste-to-energy gasification equipment, some of which use plasma arc technology to achieve the high temperatures required. Exhibit 4, which is not intended to be exhaustive, lists those companies which appear to have operational projects. We note that some projects have failed because of issues securing large volumes of waste and transporting it over a long distance to supply a single large-scale plant. Since MagneGas’s equipment is small scale, it can be located close to a source of waste, circumventing this problem.
Exhibit 4: Gasification equipment
Heading Left |
Plasma |
Status |
Size |
Feedstock |
Advanced Plasma Power |
Yes |
Pilot in Swindon, UK |
20tpd |
Municipal solid waste and commercial/industrial waste |
AlterNRG/Westinghouse Plasma |
Yes |
Commercial operation in China, India and Japan. Tees Valley project closed 2016 |
24-150tpd |
Municipal solid waste water sludge, hazardous waste |
ArcSec Technologies |
Yes |
Pilot under construction in Alabama |
11 acre site |
Multiple waste streams |
Chiinook Sciences |
No |
16 projects over the last 14 years |
N/A |
N/A |
Covanta |
No |
Demonstration plant operational at its Tulsa, Oklahoma waste-to-energy site |
375tpd |
Municipal waste |
EQTEC |
No |
Operational projects in Europe and India |
20-100tpd |
Primarily biomass |
GeoPlasma |
Yes |
Contract for project in Florida terminated prior to completion |
180tpd |
Municipal waste |
Hitachi Metals/Westinghouse Plasma |
Yes |
25tpd plant operational in Japan. 150tpd plant commissioned in Japan but closed because of problems with waste contracts |
25tpd and 150tpd |
Municipal waste and dried sewage sludge |
InEnTec |
Yes |
Operational at landfill site in Oregon. |
N/A |
Municipal waste |
PEAT International |
Yes |
National Cheng Kung University, Taiwan |
3-5tpd |
Multiple waste streams |
Plasco Energy |
Yes |
Project in Ottawa was cancelled because of lack of government funding. Company placed in administration. |
<405tpd |
N/A |
PowerHouse Energy Group |
No |
Pilot on Merseyside, UK |
C 3tpd |
Shredded plastic, tyre crumb |
PRM Energy Systems |
No |
Over 20 systems in commercial operation in the US, Europe, and South-East Asia |
20-2,000tpd |
Biomass including sewage sludge |
PyroGenesis |
Yes |
Operational on US Navy aircraft carrier |
<5tpd |
Multiple waste streams |
Shell Global Solutions |
Data |
Over 20 coal gasification plants in operation |
2,000tpd |
Coal, biomass |
Source: Edison Investment Research
Commercialising the technology
Sales channels already established in the US
Exhibit 5: Revenue FY13-17
|
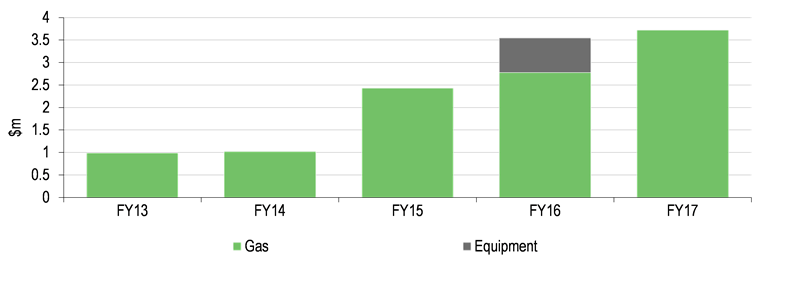
|
Source: SEC filings. Note: Equipment sale in FY16 was to Green Arc Supply.
|
Initial footprint in Florida
MagneGas first introduced its renewable metal cutting fuel in 2010 through third-party US distributors. In 2014, management decided to start selling the gas directly. Potential customers prefer to purchase their cutting gases and cutting equipment from the same supplier, so management acquired a local company, ESSI, which already sold the range of products required. The ability to offer a differentiated product such as MagneGas2 facilitates introductions to new customers who will also purchase complementary products. Between 2013 and 2017 total sales (including other cutting gases and cutting tools) grew at 39% CAGR. This compares very favourably with the conventional cutting gas market which management estimates had a CAGR of only 2-3%. Sales of complementary products are significant. Management estimates that it makes $33 ancillary sales for each $1 of MagneGas2 sold. It has taken steps to expand the portfolio of complementary products eg adding calibration gases to the offer in July 2016 and cutting tools in May 2017.
Expansion into Texas and California, the top two markets for cutting gases
Industrial gases are heavily used in the shipping, rail, oil and gas industries, by utilities, in super-ports, for demolition and for construction of heavy infrastructure. This means that Houston and the San Diego/Long Beach/Los Angeles corridor are the number one and number two markets for industrial gas in the US and California and Texas are largest markets in the US by state. The Houston area is booming as petroleum and natural gas markets continue to recover after Hurricane Harvey. San Diego has the potential to be one of the key markets given the proximity to Coronado Island and the massive US military presence, as well as a wide range of utility, commercial shipping, rail, logistics and infrastructure operators in the bay area. Management estimates that the Greater California market has the potential to generate in excess of $100m revenues annually for MagneGas. MagneGas acquired sales outlets in both of these key markets during the first four months of FY18. Management intends to make further acquisitions in these regions, providing it can do so without incurring too much share dilution, as the recent acquisitions were funded through the issue of preferred stock.
Exhibit 6: Development of US sales channels
Date |
Event |
October 2014 |
Acquisition of ESSI in Florida for $3m cash. Annual revenues of c $2m |
May 2016 |
Complete Welding and Cutting Supplies appointed as regional distributor for Mexico and Southern California |
June 2016 |
Berger Welding Supply of Indiana appointed as regional distributor, giving access to major automotive manufacturer |
July 2016 |
ESSI site opened in Lakeland, central Florida |
October 2016 |
Holston Gases appointed as distributor for Tennessee and mid-South states |
Jan 2017 |
ESSI site opened in Sarasota, Florida |
March 2017 |
Distributor Green Arc Supplies installs a gasification unit. Purchase price $775k, royalty of $0.02/cubic foot of gas |
Q417 |
Expansion of ESSI sales force |
Jan 2018 |
Acquisition of Complete Welding in San Diego, Southern California for $745k. $0.7m annualised revenues. C 100% expansion of Complete Welding sales force short term |
Feb 2018 |
Acquisition of Green Arc Supply with two locations in Texas, one in Louisiana. Consideration of $2.3m, $1.0m payable in cash, the remainder in shares |
April 2018 |
Acquisition of former distributor, Trico Welding Supplies, in Northern California for $2.0m (gross) completed |
April 2018 |
Expansion into Pasco County, Florida, giving access to Covanta operations in the region |
Improving profitability of direct sales operations
The combined scale of operations following the recent sequence of acquisitions gives MagneGas stronger purchasing power, thus improving margins, and also helps it pursue larger national accounts. We note that in March 2018, MagneGas signed its first multi-year industrial bulk gas contract, emphasising its enhanced market profile. Having a direct sales operation in a region with a high density of current and potential customers helps profitability by making it worthwhile to install gasification technology in the area rather than shipping the gas from the production facility in Florida, thus significantly reducing logistics costs. There is already a MagneGas2 production facility at one of the company’s locations in Texas. Management also intends to install one in the California region. Increasing turnover in one location also helps improve profitability as gas cylinders, which cost several times more than the gas they contain, are used and refilled more quickly, reducing the cylinder/gas overhead. This project will incur minimal capex as MagneGas will redeploy equipment that became surplus to requirements when it switched to using butanol as feedstock, thus substantially improving production efficiency. In addition, management intends to develop its own plant in Florida for filling cylinders with non-proprietary gases so it can save costs by purchasing these in bulk. Management expects that this plant will become operational by the end of FY18 and should improve gas margins by 10-15pp.
Distributors treble minimum purchases of MagneGas2
In November 2017, MagneGas announced that its three largest cutting gas distributors, Holston Gases in Tennessee, Haun Welding Supply in New York State and AWISCO in the New York metropolitan area, had all agreed to significant increases in MagneGas2 purchases. This represents a minimum three-fold increase in sales from these distributors from Q417 onwards. Now that Green Arc in Texas, which has its own MagneGas2 production equipment, is part of the group, management intends to secure new distributors in the Mid-West US who can be supplied from this facility.
Preparing for European launch
The European Union (EU) is an attractive market for MagneGas because of the Renewable Energy Directive that sets a binding target of deriving at least 20% of energy requirements from renewable sources by 2020. The EU is also, according to management estimates, the second largest market for industrial gases globally. For the last 10 years, the company has been working with Berlin-based Infinite Fuels, a developer of alternative energy production equipment that reacts biomass with electricity to produce useful hydrocarbon fuel from bio-wastes. MagneGas is in the process of forming a JV with Infinite Fuels, completion of which is dependent on the latter securing c €2m equity finance which is a requirement for it to receive a €6.0m (US$7.2m) grant from the European Commission. If successful, this will cover much of the start-up costs of launching production and sales of MagneGas2 in Germany. Management expects that this funding will act as a catalyst to attracting additional capital in Europe.
In addition to the activity with Infinite Fuels, management is evaluating setting up operations at one or more European super-ports ie Rotterdam, Amsterdam, Antwerp, Marseille, Hamburg, Copenhagen, or Calais. Each of these locations has several hundred potential users of MagneGas2, all of which are larger than the current largest single client. Super-ports in other regions, eg Dubai, Japan, Singapore and South Korea, are also near-term targets. We note that MagneGas is already actively marketing its products and services in Houston and Los Angeles. Management estimates that the potential client base in a single port area could be addressed from a team of three to five people, cost less than $1m to set-up and generating multiple millions of dollars of EBITDA a year. Such an operation would be wholly owned by MagneGas.
Launching commercial sterilisation projects
Between 2014 and 2016 MagneGas undertook a pilot study at the largest pig farm in Indiana. This verified that the process works at scale to eliminate E. coli and faecal coliforms, has a beneficial impact on total suspended solids, which is a parameter used to assess the quality of waste water and meets EPA standards. Importantly, it enables hog manure to be treated as a class A rather than class B waste so it can be used as a high-nutrient, low-odour fertiliser. Management is currently in the process of establishing a commercial pilot treating pig manure in North Carolina. Starting in Q119, it intends to monetises the technology through providing a sterilisation service and sales of manure feedstock and reclaimed water. Management estimates that there are 1,700 hog farms in the local area, collectively producing 15m tons of waste each year, which represents an attractive potential market.
In Q417, MagneGas formally launched an 18-month pilot with one of the largest dairy farms in Florida. The primary purpose of the pilot is to evaluate the efficacy of the sterilisation process for cow manure. It is jointly funded by the USDA through a $432,000 grant, which represents 50% of the pilot costs and is a key step to obtaining USDA subsidised equipment eligibility and gathering sufficient data to move ahead with commercialisation within the agricultural industry. This grant builds on the hog industry study. In May 2018, MagneGas achieved its first major milestone on the project by giving a successful live sterilisation demonstration at the farm to representatives from the USDA, the Dairy Farmers of America, the International Dairy Journal and other independent dairy operators, as well as local government representatives. MagneGas will continue to submit results from the pilot to the USDA for the remainder of the project’s duration.
In December 2017, MagneGas announced it had received a preliminary order for a sterilisation unit to be delivered into the southern Italian market in FY18. The unit will be used primarily for the sterilisation of agricultural waste. The transaction may be structured as a service contract with MagneGas receiving revenues as waste is processed. Management expects the project to be funded in part by an Italian grant designed to support waste reduction and carbon emission reductions. This order follows on from one for a small sterilisation unit from an Italian client who has verified that MagneGas’s sterilisation process positively impacts chemical oxygen demand in landfill waste water and the client intends to scale up the project.
In July 2017 MagneGas announced that one of its distributors in Italy had completed several years of using the technology to reduce the chemical oxygen demand of leachates and had placed a $140k order for sterilisation equipment. MagneGas will sell the distributor components that will be assembled according to MagneGas’s instructions. The finished unit will be installed at a purpose-built facility that will treat leachate in return for a disposal fee, which may potentially be shared with MagneGas. Following an initial period of operation, MagneGas and its distributor intend to deploy the technology on multiple sites for treating leachates throughout Italy later in 2018. The technology significantly reduces the disposal costs of landfill wastewater and represents a strong value proposition for landfill operators. Since much of the EU regulation regarding leachate is standardised, this presents a very large addressable market across much of the EU landfill industry.
A northern California municipality is currently evaluating a proposal for deploying the technology in a waste water sterilisation programme. If successful, this would represent the first for public-private partnership in the US for waste-water sterilisation, realising revenues by the end of FY18.
Launching commercial waste-to-energy projects
MagneGas is in discussions with an international medical manufacturing company. It has demonstrated that its gasification technology can convert contaminated ethanol, which is one of types of medical waste produced, into a useful fuel. This gives a route for potentially reducing the cost of MagneGas fuel by 20-25% by taking the waste ethanol as a feedstock. The volume of gas potentially produced from processing all of the waste ethanol produced by this medical manufacturing company far exceeds the amount of cutting gas that MagneGas could sell, so management has plans to convert the remainder to bio-diesel using a catalytic process. Management notes that this medical manufacturing company has another 30 types of waste stream which could potentially be pulverised and converted to useful gas in the next generation of gasification equipment (see above).