Company description: Innovative solid-state lithium battery technology
Ensurge Micropower was reborn in January 2020 when management announced that, going forwards, it would use its R2R assets and printed electronics IP to develop and manufacture miniature solid-state lithium batteries. This proven ability to print electronic components on a flexible steel substrate means that Ensurge can offer microbatteries that offer superior performance to conventional lithium-ion rechargeable batteries, thus commanding a premium price. Importantly, since Ensurge’s solid-state format is offered as a replacement for conventional coin and button batteries in hearing aids as well as addressing emerging markets such as connected sensors and sports wearables, the demand is already there, so the company does not need to build up the market itself. Management estimates that the addressable microbatteries market is over 1bn units per year and has previously noted that it would be possible for the company to have a cash-generative, profitable business on around 4m units per year, which is a very modest share of the addressable market.
Ensurge Micropower has already signed agreements with five customers. These include a Fortune 500 industrial company active in manufacturing capital equipment, a customer in the digital health market, two agreements in the medical hearables market and one in the broader wearables market. Although management had intended to ship the first samples by the end of FY21, this milestone has slipped, contributing to a share price reduction from NOK0.75 at the start of January. The company now intends to ship samples to these customers ‘in the short-term’ and to commence deliveries of microbatteries for commercial use by the digital health customer in Q422.
Ensurge differs from many early-stage technology companies in already having a volume manufacturing facility, which it has used to make other printed electronics components. Prior to the decision in January 2020 to develop printed microbatteries, previous management had installed an R2R production line in San Jose. This had output several million electronic article surveillance (EAS) tags and was preparing to commence production of more complex near field communication (NFC) tags before it was mothballed in early 2019 when it was clear that adoption of NFC tags by brand owners for brand protection and marketing purposes was not going to take off as quickly as initial customer wins had indicated.
The company’s corporate headquarters are in Oslo, Norway, and its global headquarters are at its high-capacity flexible electronics manufacturing site in San Jose, California. The company’s shares were admitted to listing at the Oslo Axess in January 2008 and to the Oslo Børs in February 2015. Its American depository receipts (ADRs) commenced trading in the US on the OTCQX market in March 2015. This US listing was transferred to the OTCQB Venture Market in June 2020.
Advantages of solid-state lithium batteries
Lithium-ion battery technology has become increasingly popular because of its relatively high energy density. This means that a conventional lithium-ion battery can be half the size of a nickel cadmium battery and still store the same amount of charge. A solid-state lithium battery goes further, storing around double the charge of a conventional lithium-ion battery. This improvement is achieved by replacing the liquid or polymer gel electrolyte of a conventional lithium-ion battery with a solid material, usually either a ceramic or a solid polymer, although sulphides and glass are also used. Solid-state batteries also charge at twice the speed of conventional lithium-ion batteries, retain the charge for longer and last for two to three times the number of charge/discharge cycles. All of these factors are desirable when choosing batteries for use in applications such as wearables and sensors where minimising size and weight as well as maximising battery longevity are important. Critically for applications where batteries are close to the body, eliminating the liquid electrolyte, which is highly flammable, makes batteries safer. In addition, since all the parts are solid, the resultant batteries can also be produced in unconventional formats such as wires, ribbons or flexible patches, which gives designers of wearable devices the flexibility to create products that are more comfortable to wear. This contrasts with conventional lithium-ion batteries, where products have to be designed around existing coin or button format battery cells. From Ensurge’s point-of-view, the ability to offer customised formats also improves customer retention.
Billion-unit end market
Management expects that Ensurge’s R2R manufacturing technique would enable it to offer solid-state lithium microbatteries at a price that is similar to conventional lithium-ion batteries if required. However, it is focusing initially on those sectors where the high energy density and thin form factor enabled by the technology are most sought after and can command premium pricing, thus maximising the EBITDA potential of the existing manufacturing capacity.
Exhibit 1: Microbatteries market in 2025 (1.3bn units)
|
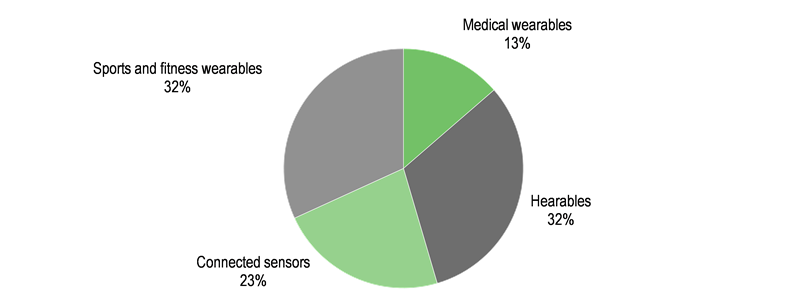
|
Source: Ensurge estimates based on sources including IDTechEx
|
Ensurge is concentrating on the medical wearables and hearables markets to start with, followed by the connected sensors and sports wearables markets, which are at an earlier stage of evolution. All four markets require microbatteries capable of holding between 1–70 milliwatt hours (mWh) of energy and having a volumetric energy density of 600–1,000Wh/litre. This is achievable using Ensurge’s existing chemistry. Referencing research from IDTechEx, management notes that these markets are predicted to grow to over 1bn batteries per year by 2025.
Hearables (addressable market of 560m units/year): this application includes hearing aids and wireless earbuds. Hearing aids are transitioning from 15–25mAh capacity non-rechargeable batteries to conventional lithium-ion batteries, which are rechargeable. However, conventional rechargeable batteries only last through 300–400 charge/discharge cycles, which is around a year if the battery is recharged overnight while the wearer is asleep. In contrast, a solid-state lithium battery will last for over 1,000 charge/discharge cycles, or around three to four years. Once the rechargeable battery reaches its cycle limit, typically the user has to send the hearing aid to the supplier to have the battery replaced, the cost of which may be covered by the supplier as part of the service warranty. Using a solid-state microbattery instead of a conventional lithium-ion battery potentially saves on service costs, supporting the payment of a premium for the solid-state option. The energy density and number of recharge cycles becomes even more important for smaller format invisible-in-the-canal and in-the-canal hearing aids. Wireless earbuds require cells of 40–70mAh capacity and already use rechargeable batteries.
Medical wearables (addressable market of 150m units/year): this application includes continuous glucose monitors, cardiac monitors, temperature monitors, physiological monitors, glaucoma detectors and motion sensors. Here patient comfort is a priority so replacing a coin (3.2 millimetres (mm) thick) or button (4.6mm thick) cell with a device that is not only half the volume but also available as a thin (0.05–0.5mm) patch that conforms to the shape of the body or the eyeball or is in the form of a ring is a significant advantage. Eliminating concerns about a battery in close proximity to the body bursting into flames is also critical. In addition, given the relative longevity of solid-state lithium batteries, substituting a conventional lithium-ion battery with a solid-state one means that the total cost of batteries over the lifetime of the wearable is likely to be reduced. In December 2021 MarketsandMarkets published a report predicting that the global wearable healthcare market would grow from $16.2bn in 2021 to $30.1bn by 2026, a CAGR of 13.2%. The market was already showing significant growth prior to the coronavirus pandemic because of a combination of a rising geriatric population, the increasing prevalence of chronic diseases such as diabetes and the availability of advanced medical devices including wearable medical devices that have enabled the delivery of quality care in non-hospital settings. The coronavirus pandemic has accelerated the use of medical wearables because data from wearable devices can be used to alert users when changes in their metrics match those associated with COVID-19 or other diseases. The use of artificial intelligence (AI) to analyse data from wearable medical devices and the growing availability of 5G networks to transmit large quantities of data in real-time are likely to support further demand growth.
Sports and fitness wearables (addressable market of 350m units/year): this application includes small electronic devices for activity measurement and smart apparel that can carry out a wide range of functions such as monitoring vital signs or sleep patterns, regulating body temperature, checking whether an athlete’s muscles are being overworked during training or disguising a personal alarm. Comfort is possibly even more important here than in the medical wearables markets, since wearing the monitor is discretionary. A report from Data Bridge Market Research published in September 2021 predicts that the global wearable devices in sports market will grow with a CAGR of 17.6% between 2021 to 2028 to reach $44,825m by the end of the forecast period.
Connected sensors (addressable market of 240m units/year): this application includes environmental sensors, smart commercial buildings and smart manufacturing. Here the goal is to integrate miniature (1–50mAh) batteries with energy harvesting devices, namely, small solar panels that top-up the charge during the day or piezo-electric crystals, so that a wireless sensor can be installed in a hard-to-reach area such as wind turbine blade and then left for several years without incurring the cost of a maintenance person replacing the battery. This approach requires a battery that can undergo multiple thousands of charge/discharge cycles over a lifetime of five to 20 years before needing to be replaced, so a solid-state battery becomes a more cost-effective option than a conventional lithium-ion battery. These types of applications also require batteries that can withstand temperatures of -20°C to +85°C, which conventional lithium-ion batteries do not.
Competitive environment
Deposition of components on stainless steel substrate in volume is proven
Ensurge’s process for making solid-state lithium batteries is based on the anode-less solid-state battery technology developed by Oak Ridge National Laboratory (ORNL) in the United States during the 1990s, which is no longer under patent. This technology has been shown to charge rapidly and to have a lifetime of over 1,000 charge/discharge cycles. Ensurge has adapted this technology so that the layers forming the battery are printed on a very thin steel substrate that has been treated with a proprietary barrier technology so that electronic components can be printed on it. Since steel is available as very thin foils, this a battery where the substrate takes up a smaller proportion of the total volume, immediately improving energy density by c 30% compared with using silicon substrates as used by Cymbet and Ilika. Moreover, manufacturing batteries on a silicon substrate is more complicated because it requires additional processing steps to make the silicon substrate, which comes in a standard thickness, thinner. Having a steel support rather than part of a silicon wafer means that the battery is flexible and durable and can easily be made in unusual shapes such as rings. In contrast, silicon wafers are brittle and crack easily. Since steel is naturally air- and water-tight the substrate is a good packaging material, preventing moisture or oxygen from reacting with the lithium metal forming the battery anode. This means fewer layers that only provide a packaging function are required, which also improves energy density. It is also relatively easy to stack cells made on a steel substrate.
Exhibit 2: Structure of Ensurge’s solid-state lithium battery (in use)
|
Exhibit 3: Cycle life comparison
|
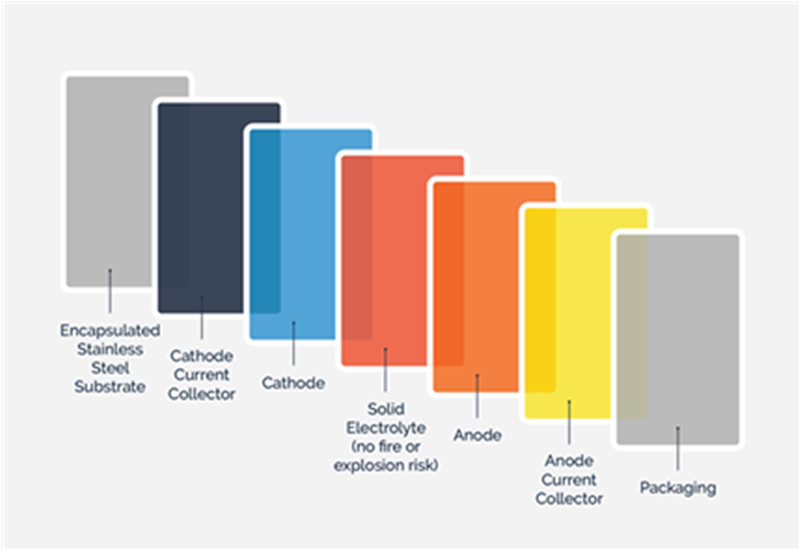
|
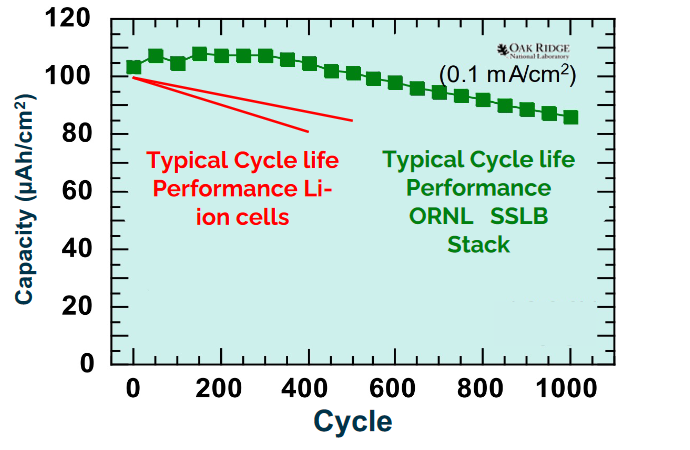
|
Source: Ensurge Micropower
|
Source: Ensurge Micropower capital markets presentation January 2022
|
Exhibit 2: Structure of Ensurge’s solid-state lithium battery (in use)
|
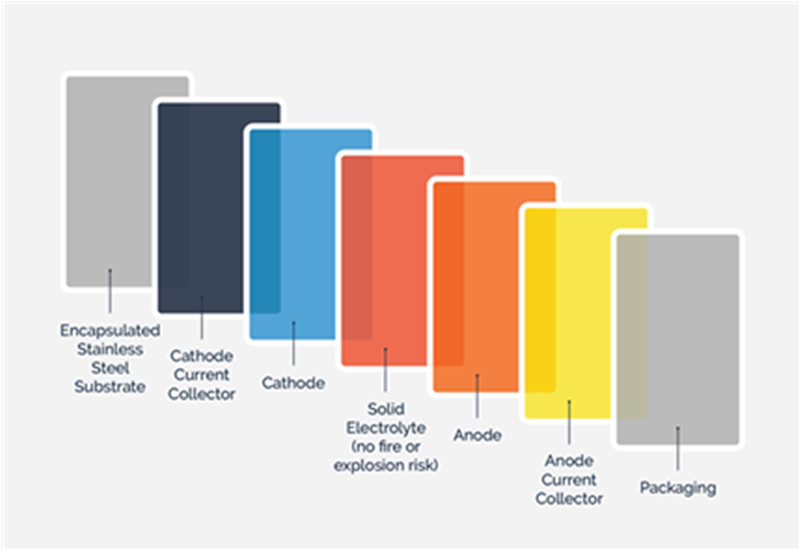
|
Source: Ensurge Micropower
|
Exhibit 3: Cycle life comparison
|
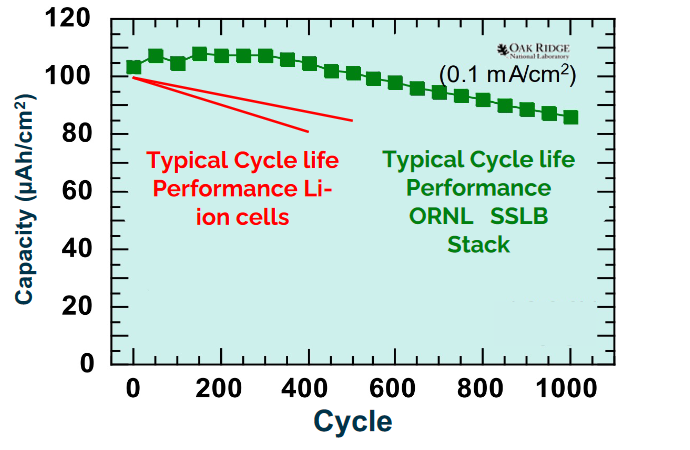
|
Source: Ensurge Micropower capital markets presentation January 2022
|
Ensurge has already proved that it can manufacture high-performance electronics components in volume on the steel foil substrate through the manufacture of several million EAS tags. While it has not manufactured solid state batteries in volume yet, the battery manufacturing process uses a subset of already proven manufacturing processes and installed equipment, thereby minimising the risk of new technology implementation.
Ensurge already has volume manufacturing facility
Management has previously estimated that Ensurge’s existing R2R facility, in which it invested over $40m for the production of EAS and NFC tags, has the capacity to output around 50m milliamp-hour class microbatteries per year, depending on the distribution of battery capacities. The company does not need any material capital expenditure to modify any of the existing tools for battery production. This means that it does not need to raise finance to fund the capacity expansion required to move to volume production or alternatively to find a manufacturing partner that will take a share of the profits. This position is in contrast with AIM-listed Ilika, which only has the capacity to produce 350,000 batteries/year from its Stereax microbattery pilot line, which management notes represents an expected revenue generating capability at peak capacity of £12m per annum.
Exhibit 4: R2R deposition at Ensurge’s facility in San Jose
|
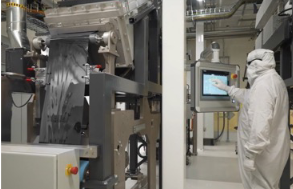
|
Source: Ensurge Micropower
|
Economic benefits of the R2R process
A continuous R2R process is much more cost-effective than processing batches of individual silicon wafers. We note that ceramic substrates are brittle and therefore unsuitable for use in R2R production processes.
Competitors not addressing mWh category
Our review of the competitive landscape shows that other companies developing solid-state batteries address applications that require either less power than Ensurge’s batteries can potentially provide or substantially more power so they are suitable for electric vehicles (EVs). Exhibit 5 summarises companies offering microbatteries, not larger batteries for EVs, so it excludes companies such as Solid Power and QuantumScape, which are focused on the EV market.
Exhibit 5: Competitive review of companies developing microbatteries
Company |
Charge capacity |
Substrate |
Commercial status |
Capacity |
Cymbet |
0.005mAh and 0.05Ah |
Silicon |
Shipping |
Volume capacity through X-fab |
Ensurge Micropower |
1mAh+ |
Flexible steel |
Samples available later in 2022 |
c 50m units/year |
FDK Corporation |
0.5mAh |
Not specified |
Samples delivered 2019 |
Not specified |
Front Edge Technology |
0.1–1.0mAh and 0.5–5.0mAh |
Flexible |
Samples delivered |
Annual capacity of 200,000 pieces of 1mAh under construction |
Ilika |
0.25mAh available 0.3mAh under development |
Silicon |
Samples delivered |
350,000 batteries/year |
Iten |
0.25mA and 0.5mAhh |
Not specified |
Shipping |
10m units/year in December 2018 with potential to increase this fivefold |
TDK Corp |
0.1mAh |
Not specified |
Shipping |
Not specified |
Source: Edison Investment Research, company websites