Company description: Machine vision solutions
STEMMER IMAGING Group (SI) is an independent provider of machine vision technology. (Machine vision is the technology required to extract actionable information from an image.) It sources system components such as industrial cameras, lenses, lighting, image capturing products, vision processing software, computers and specialist connectors from around 200 suppliers, as well as developing its own software, which enables rapid, reliable creation of machine vision solutions. Collectively, these cover the entire range of components required to produce a bespoke imaging solution. Around 70% of total revenues are generated from the creation of complex machine vision solutions in which SI combines and configures in-house and sourced components to create bespoke systems, adding value to the basic distribution proposition. Around 30% is generated from the resale of components, with SI typically advising customers on component selection as part of the process, again adding value to the basic distribution proposition. This value-add dimension is highly beneficial for both margins and customer retention. SI’s independence with regard to component selection combined with extensive industry experience allows it to offer customers the ideal solution for the requested customer application. SI serves c 3,400 customers across a wide range of industries, making the group independent of the fortunes of an individual industry or customer.
Exhibit 1: Market position
|
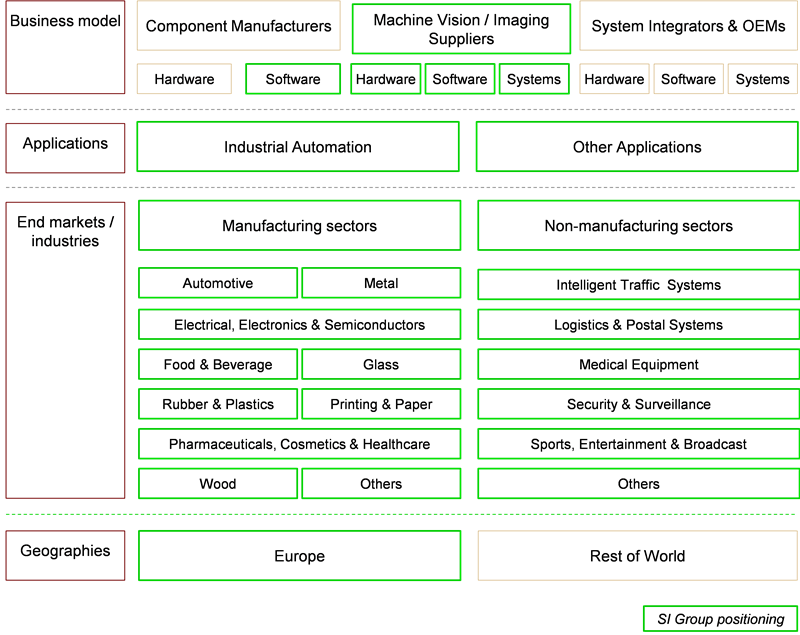
|
|
SI AG was founded in 1987. In 2017 its majority owner and founder, Wilhelm Stemmer, retired and sold his 85% stake in SI AG to SI Holding, an investment vehicle owned by Primepulse, a family investment company. As part of this transaction, SI Holding/Primepulse acquired the remaining 15% stake in SI AG that had previously been held by other members of senior management and then allowed management to purchase shares in the newly formed SI Holding. SI AG listed on the Scale index of the Deutsche Börse on 27 February 2018. As part of the listing process SI AG raised €51m (gross) at €34.0/share from the issue of new shares and SI Holding/Primepulse reduced its stake, selling 1.5m existing shares (including overallotment option), while retaining a majority holding. The placing was significantly oversubscribed. The funds raised by the company will be used to finance future acquisitions and for product development, primarily of software (see IPO section).
The group employs over 260 people, around 70% of whom have a technical background. It is headquartered near to Munich, Germany. From there it has expanded in Europe through a sequence of acquisitions (Exhibit 2). It now has local sales offices in each of its core markets: Belgium, Denmark, Finland, France, Germany, Ireland, the Netherlands, Poland, Sweden, Switzerland and the UK. Collectively, these give access to most of the regions in Europe where there is demand for machine vision technology. The headquarters site also houses the customer training centre, laboratories for feasibility studies, international technical support, software development, cable manufacturing, procurement, warehousing and logistics.
Date |
Event |
1973 |
STEMMER ELEKTRONIK founded |
1975 |
First machine vision system delivered |
1987 |
STEMMER IMAGING founded |
1997 |
Common Vision Blox (CVB) software launched |
2000 |
Customer training programme expanded |
2002 |
Cable production started |
2004 |
Firstsight Vision acquired in the UK Sales operation in Switzerland launched Imasys acquired in France Logistics centre opened |
2010 |
SI training centre, European Imaging Academy, opened |
2012 |
Iris Vision acquired in the Netherlands |
2014 |
Parameter acquired, serving the Nordic region |
2015 |
Image House in Denmark acquired and integrated with Parameter |
2017 |
Founder Wilhelm Stemmer retires and sells 85% stake to SI Holding, part of Primepulse |
2018 |
Acquisition of Data Vision, Netherlands Listing on Scale segment of Deutsche Börse |
Date |
1973 |
1975 |
1987 |
1997 |
2000 |
2002 |
2004 |
2010 |
2012 |
2014 |
2015 |
2017 |
2018 |
Event |
STEMMER ELEKTRONIK founded |
First machine vision system delivered |
STEMMER IMAGING founded |
Common Vision Blox (CVB) software launched |
Customer training programme expanded |
Cable production started |
Firstsight Vision acquired in the UK Sales operation in Switzerland launched Imasys acquired in France Logistics centre opened |
SI training centre, European Imaging Academy, opened |
Iris Vision acquired in the Netherlands |
Parameter acquired, serving the Nordic region |
Image House in Denmark acquired and integrated with Parameter |
Founder Wilhelm Stemmer retires and sells 85% stake to SI Holding, part of Primepulse |
Acquisition of Data Vision, Netherlands Listing on Scale segment of Deutsche Börse |
Missing link between hardware and application
SI’s core competence is the customisation, modification and adaptation of machine vision systems to customer specific needs. Around two-thirds of group sales are generated from customer-specific configurations of complex machine vision products compared with one-third from resale of components to OEMs. SI has developed its own interface for controlling cameras, imaging software and cabling to enable it to create complete systems. Around 10% of revenues are derived from the provision of software, services and other products developed in-house.
SI recognised early on that software is a crucial component for machine vision and introduced its own library of imaging software, Common Vision Blox (CVB), in 1997. CVB helps customers create machine vision solutions tailored for specific production process requirements. It acts as an interface between cameras and the control elements of a machine vision system, interpreting the data from the camera, for example recognising bar codes and text. The software is suitable for many industries. Importantly, it is compatible with all major hardware components and all interfaces, encouraging adoption. The standard software licence is included in some cameras delivered by SI Group and provided to the customer free of charge. Charges are made for software licences, providing enhanced functionality such as X-ray applications. SI develops customer-specific software products for its clients for new or especially complex applications on request. Currently 60-70% of SI's customers use CVB. The software is active in over 75,000 applications.
SI manufactures and tests cables that meet the specific requirements of machine vision systems. These have the appropriate connectors, can withstand repetitive movements when attached to robotic arms and are suitable for harsh industrial environments. This is too small an application area to be of interest to manufactures of standard cables. Competitors in the machine vision market do not have the scale to be able to offer this. Over 2,000 different kinds of vision cables are produced and tested per year. Cables are sold as part of complete solutions or as standalone products.
The customer offer includes services such as pre- and post-sales support, feasibility studies to validate products and systems before delivery, development services and customer training to support clients at every phase of a project. Management is keen to increase the proportion of revenues attributable to services, in part because this will have a beneficial impact on margins, in part because splitting out services as a separate revenue stream will encourage employees to charge for services where appropriate.
Switzerland-based Leuthold Mechanik (HLM) builds machines that manufacture aluminium containers used, for example, in pet food packaging. Container walls must be as thin as possible to reduce material usage and thus cost, but if the walls get too thin there is greater risk of holes and leaks. The trays are pressed in batches of four at a rate of 480 trays per minute. The quality control module consists of four parallel lines with offset imaging stations. The LED lighting and cameras on each line are triggered by a light barrier as each tray approaches. Genie Nano cameras from Teledyne DALSA located underneath each conveyer belt inspect the containers from below using backlights. As no standard illumination was able to meet all the requirements, SI developed a dedicated LED illuminator for the project. The solution inspects 120 images per minute on each track, ie at the same rate as the trays are pressed out. The CVB software is used to analyse the image and communicate whether each tray is of acceptable quality or not. SI delivers all the components to HLM preconfigured and tested, considerably reducing the cost to HLM of building the quality control system. SI has delivered over 700 complete systems to HLM since 2008 and been engaged for follow-on projects.