Company description: High-tech white powders
Nabaltec manufactures specialist inorganic chemicals that are used as halogen-free, flame retardant fillers; ceramic raw materials used in the refractory industry, technical ceramics and abrasives; and highly specialised ceramic raw materials used in ballistics protection. Its annual capacity totals around 250,000 tonnes.
Nabaltec’s output is used in a diverse range of applications, many of which have been selected by management because they offer the opportunity for higher growth than the average for the German chemical industry as a whole. For example, demand for halogen-free flame retardants is growing because they reduce the production of hazardous fumes in the event of fire and are not subject to stringent regulations when disposed of because they do not contain hazardous substances such as bromine. Demand for higher purity aluminium oxide used to make the linings of steel manufacturing kilns is rising because the use of the oxide results in longer lasting linings, which improves steel manufacturing efficiency. Management estimates that Nabaltec is number one in the global market for functional fillers based on fine precipitated aluminium hydroxide and number three in Europe for technical ceramics. The company has achieved this position through its ability to supply consistently high-quality chemicals that result in technically superior end-products, the breadth of its product portfolio, its ability to develop patentable product applicable to niche growth segments and investment in capacity.
Nabaltec was formed in 1995 through the spin-off of the specialty alumina division of VAW aluminum AG and listed on the German Stock Exchange in 2006. It is headquartered in Schwandorf, Germany, where its European volume manufacturing facility is located. The other sites are in Kelheim, Germany, where there is a pilot plant for product development, and Corpus Christi, US, which is set up for volume manufacturing of fine precipitated aluminium hydroxide functional fillers. Nabaltec has a global network of around 60 agents, through which it supplies c 800 customers in around 60 countries. In FY16 73% of revenues were derived from exports. Nabaltec employs over 450 people.
Revenues by division/geography
Exhibit 1: FY16 revenue split by division
|
Exhibit 2: FY16 revenue split by geography
|
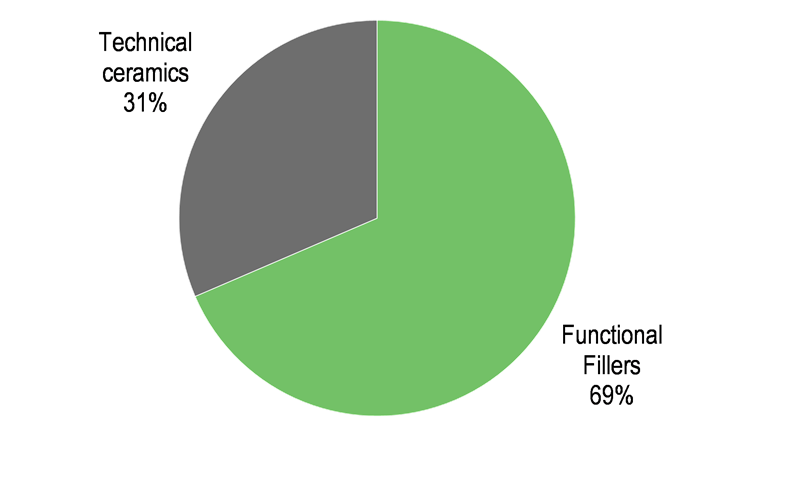
|
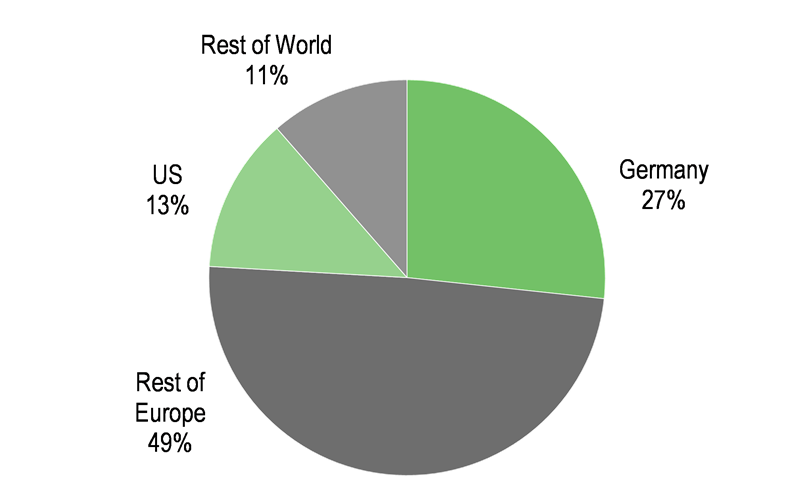
|
|
|
Exhibit 1: FY16 revenue split by division
|
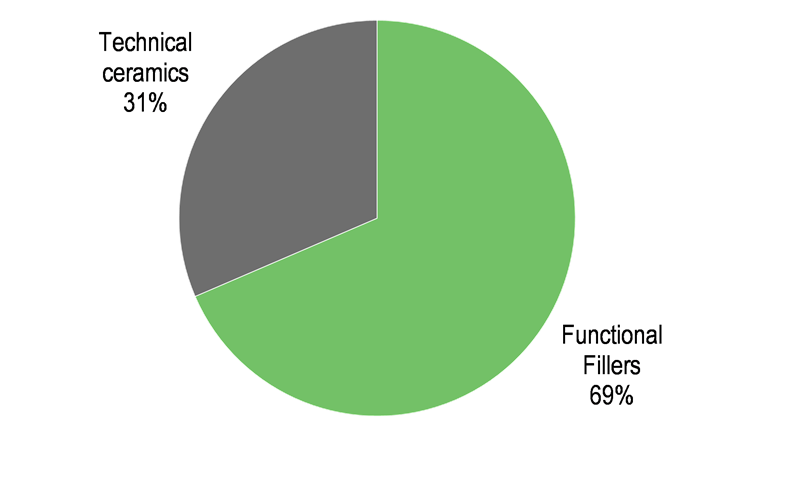
|
|
Exhibit 2: FY16 revenue split by geography
|
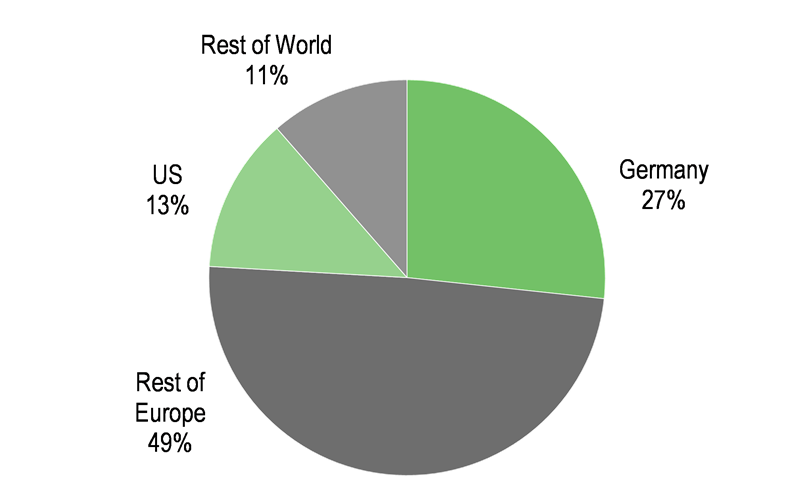
|
|
Business description
Functional Fillers
Nabaltec manufactures a range of flame retardants based on metal hydrates, primarily aluminium hydroxide, which is sold under the APYRAL brand. When plastic containing the retardant is exposed to a flame, the aluminium hydroxide splits into aluminium oxide and water. The endothermic process absorbs energy from the ignition source and the water vapour released cools the surface of the plastic and dilutes any flammable gases in the surrounding area. The aluminium oxide residue acts as a barrier to prevent the release of further particulates from the plastic. It also shields the plastic from heat, which could cause further decomposition. Smoke reduction is particularly important for plastics such as PVC (polyvinyl chloride) as they release black, toxic smoke when burned. The retardant fillers make plastics safer without compromising the performance of the consumer product in which they are used.
Aluminium hydroxide is suitable for applications up to 200°C, while magnesium hydroxide is used for higher temperatures (up to 300°C). For the highest temperatures, ie up to 320°C, a newer material, aluminium oxide hydrate or boehmite, is used. Boehmite is supplied for use as a raw material in the manufacture of catalysts used in petrol refining. It is beginning to be used as a flame retardant in the plastic substrate of printed circuit boards and as the coating of separators in lithium-ion batteries, which improves thermal stability, thus improving battery safety. These batteries are key elements in electric powered vehicles and energy storage systems used in conjunction with renewable energy sources.
Exhibit 3: Analysis of application areas for Functional Filler products
|
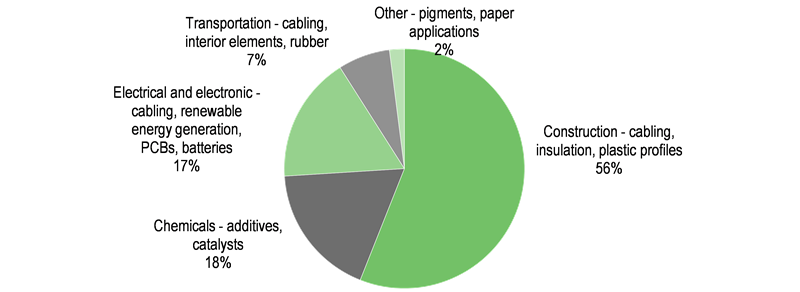
|
|
Demand for non-halogenated flame retardants is growing because of tightening fire safety requirements and increasing attention on the reduction of fumes. This is of particular concern in areas where it is difficult for people to escape quickly, such as tunnels, airports and high-rise buildings and for electronic products that may be taken onto aircraft. In July 2017, the Construction Products Regulation comes into force throughout the EU. This makes it mandatory for new cabling supplying electricity or being used for control or communication purposes to meet the EN 50575 standard regarding performance when subjected to fire. In addition, the enhanced RoHS (Restriction of Hazardous Substances) directive, which comes into force in July 2019, bans the use of polybrominated biphenyls and polybrominated diphenyl ether as flame retardants for plastics in most electronic goods. Polybrominated biphenyls were withdrawn from the market in the early 1970s because of concerns about toxicity. Currently 18% of plastics are treated with halogenated flame retardants compared with 12% (source: Arbeitsgemeinschaft PVC und Umwelt, EFRA) that are treated with halogen-free flame retardants, giving ample opportunity for growth as the industry switches to halogen-free substances. A report published by the Freedonia Group in 2015 noted that the global market for flame retardants totalled 2.2m tonnes in 2013, of which 31.8% (c 700k tonnes) were based on aluminium hydroxide. The report forecast a 4.4% CAGR for aluminium hydroxide type retardants through to 2023. In contrast, production volumes for the German chemical industry as a whole rose by only 0.5% year-on-year during 2016 but prices fell by an average of 3%. (source: VCI (Verband der Chemischen Industrie eV)).
Nabaltec is the world-leader with regards to the volume of fine precipitated aluminium hydroxide sold as a functional filler. This places it ahead of Huber Engineered Materials, CHALCO, INOTAL and KC Corporation. It has achieved this position through the quality and reliability of its products, its long-term relationship with customers and sustained investment in R&D and capacity.
Technical Ceramics
Nabaltec offers a wide range of specialist branded aluminium oxides, which are used as raw materials for various applications in the ceramics industry. It also manufactures products tailored to specific customer requirements. Aluminium oxide is used in the manufacture of industrial ceramics because the resultant ceramic material has good insulation properties, is very hard and can withstand extreme changes in temperature without expanding or contracting, which improves the lifetime of products. Aluminium oxide powder is also used in high-performance applications outside the ceramics industry, eg as a replacement for asbestos in brake linings, engine catalysts and for polishing powders. Nabaltec’s materials are characterised by their highly consistent properties, which result in enhanced mechanical, thermal, electrical and chemical performance of the finished ceramic products.
Exhibit 4: Analysis of application areas for Technical Ceramics products
|
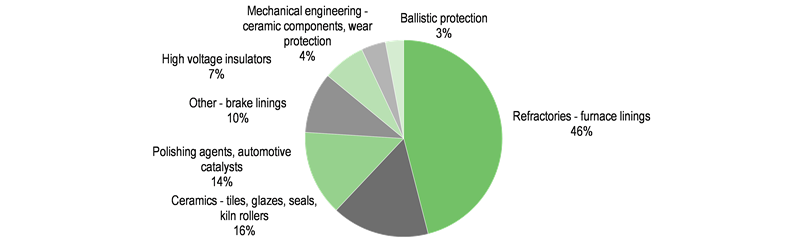
|
|
Nabaltec also offers semi-finished, ready-to-press ceramic bodies based on its own aluminium oxides with additional mineral dopants chosen as appropriate for specific applications. These high-performance ceramics have low shrinkage properties so the dimensions of the finished shape are the same as those defined by the mould, as well as extremely high mechanical strength. Their low weight and extremely high hardness makes them suitable for use as ballistic protection for personnel and vehicles. Their resistance to wear and chemical attack makes the ceramic bodies ideal for seals and other components used in the chemical industry. Their electrical insulating properties and high thermal conductivity make them valuable materials in the electrical engineering and electronics industries. The ceramic material is also resistant to high temperatures, temperature cycling and wear.
Nabaltec is the third largest supplier of technical ceramic materials in Europe, behind Almatis and Alteo, but ahead of Silkem and Huber Engineered Materials. Similarly to the Functional Fillers segment, Nabaltec has achieved this position through the quality and reliability of its products, its long-term relationship with customers and its sustained investment in R&D and capacity. Around half of Nabaltec’s technical ceramic output goes to refractories, where it helps support efficient and sustainable steel production. There is a big difference between the consumption of high-performance speciality aluminas per tonne of steel in Japan (1.3-1.5kg/tonne), which has the most advanced technology, Russia and Central Europe (0.7-0.8kg/tonne), and China and India (> 0.4kg/tonne). This suggests there is potential for the wider adoption of longer-lasting refractories based on higher purity aluminium oxide (referred to as reactive aluminium oxide), were China and India to shift to more efficient production techniques. A report from Roskill published in 2016 noted that the global speciality aluminium oxides market totalled 2.815m tonnes in 2015 and forecast a CAGR of c 4% until 2021, driven primarily by demand for refractory materials. Nabaltec is the market leader globally in ready-to-press aluminium oxide-based ceramic bodies. However, we note that this market is relatively small, with the principal competition being from companies manufacturing the ceramic bodies in-house.
Market-leading positions in growth markets
Nabaltec has identified markets that have good growth prospects (as discussed above) and seeks market-leading positions within these markets. Management estimates that Nabaltec is the largest provider globally of flame retardant fillers based on fine precipitated hydroxides (see above) and is the third largest provider in Europe for aluminium oxide used in refractories, technical ceramics and abrasives and is seeking to grow this area of the business. It is already the market leader globally in ready-to-press ceramic bodies, having invested in a state-of-the-art production facility for these in Schwandorf, although this is a very niche market. The key to achieving these market-leading positions is Nabaltec’s reputation as a reliable supplier of consistently high-quality and innovative materials, which underpins its long-term relationship with customers. In addition, Nabaltec has had access to funding that has enabled it to invest in capacity and product development. It has invested more than €160m in infrastructure since 2006. The need for relatively high levels of investment in this industry is a significant barrier to entry.
Globalisation
As the markets served are global, Nabaltec has developed sales channels to address this. In addition to the network of agents, it established a direct sales office in Japan in Q116 to serve the Asia-Pacific market. North American customers are served more efficiently from the Corpus Christi facility, when operational, because the cost of transporting functional filler material and lower value technical ceramics materials is relatively high compared to the sales price.
Product portfolio expansion
Nabaltec is constantly looking for ways to add new products to its portfolio. Through its participation in various European industry bodies, the company is able to identify major trends in its primary markets at a very early stage and on a global scale. It also works closely with customers to develop products optimised to their requirements, by either modifying the qualities of existing products to meet specific needs, or evaluating new applications for existing materials. Nabaltec often undergoes long and intensive approval procedures with its customers, especially for new products. This typically leads to long-term supply relationships and constitutes a significant barrier to entry. Examples of new products include boehmites, which offer flame retardant properties at even higher temperatures, softly calcined aluminium oxides for use in high-quality abrasives, raw materials for alternative energy storage and electric vehicles and Nabacast, a new class of patented cement free materials for making longer-lasting refractories.
Swift response production planning
Since it takes time to switch from one production process to another, Nabaltec has implemented a customised system for planning work and assigning batches with different volumes to equipment of the appropriate capacity. This enables it to optimise margins when demand fluctuates and batch sizes change.
In August 2016, Nabaltec suspended production of fine precipitated aluminium hydroxide at its US subsidiary, Nashtec, because its main supplier of raw materials in the US, Sherwin Alumina, was obliged to discontinue output because of Chapter 11 proceedings. Since then, Nabaltec has supplied its customers in North America with product manufactured in its European facilities. In March 2017 Nabaltec acquired the outstanding 49% in Nashtec that it did not already own. Management has already begun to retool the site with the intention of resuming supply to US customers from the site in early 2018.
Johannes Heckmann (CEO)
Mr Heckmann was appointed CEO in January 2017. He has been a member of management at Nabaltec since 1995 and was appointed to the management board with responsibility for production and R&D at the time of the IPO in 2006. Prior to joining Nabaltec, Mr Heckmann worked as a project manager for AKW Amberger Kaolinwerke and at Schindler Aufzüge.
Günther Spitzer (CFO)
Mr Spitzer was appointed CFO in January 2017 and is responsible for finance, administration and HR. He joined the business that would become Nabaltec, VAW aluminium’s Schwandorf plant, in 1985 as a commercial employee, became the head of the finance department in 1998 and director of finance in 2009.
Dr Michael Klimes (COO)
Dr Klimes was appointed COO in January 2017 and is responsible for R&D/technical service, production and sales. On completion of his chemistry studies, he joined the Speciality Alumina division of VAW aluminum AG in 1992 as a sales manager. In 1995 he became the hydroxides sales manager at Nabaltec and has headed the Functional Fillers division since 2007. He served as chairman of the Phosphorus, Inorganic and Nitrogen Flame Retardants Association from 2009 to 2016 and is now vice chairman of the organisation.
The shareholder list is dominated by two families: that of the current CEO, Johannes Heckmann, and that of Gerhard Witzany, who retired from the management board in December 2016. The largest institutional investor, Invesco, holds a 5.1% stake.
Exhibit 5: Significant shareholders
Shareholder |
Holding |
Heckmann family |
31.2% |
Witzany family |
29.9% |
Invesco |
5.1% |
VPB Finance SA |
4.7% |
LRI Invest SA |
3.3% |
Exhibit 6: Financial summary
€000s |
2014 |
2015 |
2016 |
2017e |
2018e |
2019e |
Year end 31 December |
|
IFRS |
IFRS |
IFRS |
IFRS |
IFRS |
|
Profit & loss |
|
|
|
|
|
|
|
Revenue |
|
|
143,335 |
151,346 |
159,215 |
165,500 |
176,000 |
188,500 |
EBITDA |
|
|
22,369 |
24,691 |
22,909 |
26,550 |
29.250 |
32,400 |
Operating Profit |
|
12,673 |
14,521 |
12,230 |
15,500 |
18,050 |
21,250 |
Profit Before Tax (FRS 3) |
8,522 |
10,850 |
9,162 |
12,350 |
15,050 |
18,600 |
Tax |
|
|
(2,451) |
(3,408) |
(3,878) |
- |
- |
- |
Profit After Tax |
|
6,071 |
7,442 |
5,284 |
7,400 |
8,100 |
9,910 |
|
|
|
|
|
|
|
|
|
Average number of shares outstanding (m) |
8.0 |
8.0 |
8.0 |
- |
- |
- |
EPS (€) |
|
|
0.69 |
0.84 |
0.67 |
1.02 |
1.26 |
1.57 |
Dividend per share (€) |
|
0.12 |
0.15 |
0.15 |
0.19 |
0.30 |
0.37 |
|
|
|
|
|
|
|
|
|
Balance sheet |
|
|
|
|
|
|
|
Fixed Assets |
|
112,499 |
117.108 |
127,013 |
- |
- |
- |
Current Assets |
|
66,314 |
84,784 |
75,685 |
- |
- |
- |
Total assets |
|
178,813 |
201,892 |
202,698 |
- |
- |
- |
Equity |
|
52,461 |
58,102 |
57,765 |
- |
- |
- |
Non-current liabilities |
|
88,960 |
101,621 |
111,520 |
- |
- |
- |
Current liabilities |
|
|
37,392 |
42,169 |
33,413 |
- |
- |
- |
Total equity + liabilities |
|
|
178,813 |
201,892 |
202,698 |
- |
- |
- |
|
|
|
|
|
|
|
|
|
Cash flow |
|
|
|
|
|
|
|
Operating Cash Flow |
|
22,042 |
22,448 |
29,829 |
- |
- |
- |
Net Cash Flow |
|
(2,886) |
14,667 |
(6,279) |
- |
- |
- |
Closing net debt/(cash) |
|
44,163 |
41,276 |
36,386 |
33,600 |
38,100 |
24,500 |
Source: Nabaltec accounts, consensus estimates from Bloomberg
Nabaltec’s successful FY15 revenue performance carried over into FY16 as both divisions showed modest growth. However, profitability was adversely affected by a one-off non-cash adjustment to pension reserves and the temporary closure of the US subsidiary, Nashtec, in August 2016. Since then, Nabaltec has supplied its customers in North America with product manufactured in its European facilities, which has resulted in increased costs and a reduction in EBIT.
Income statement
Exhibit 7: Revenue and margin progression
|
Exhibit 8: Revenue and capex development
|
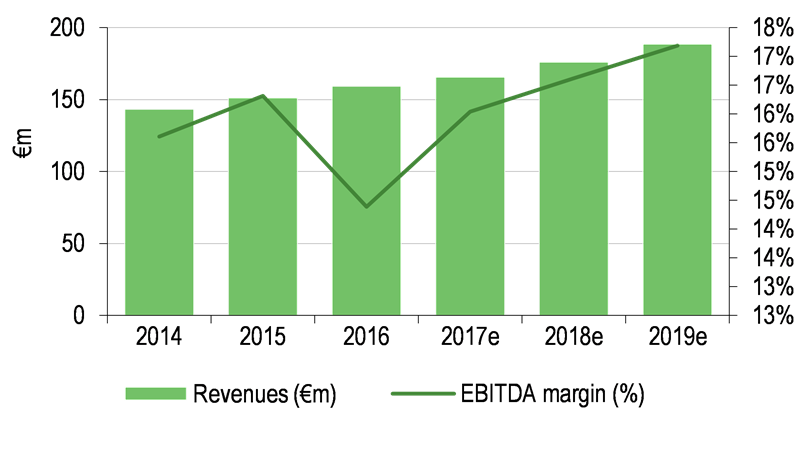
|
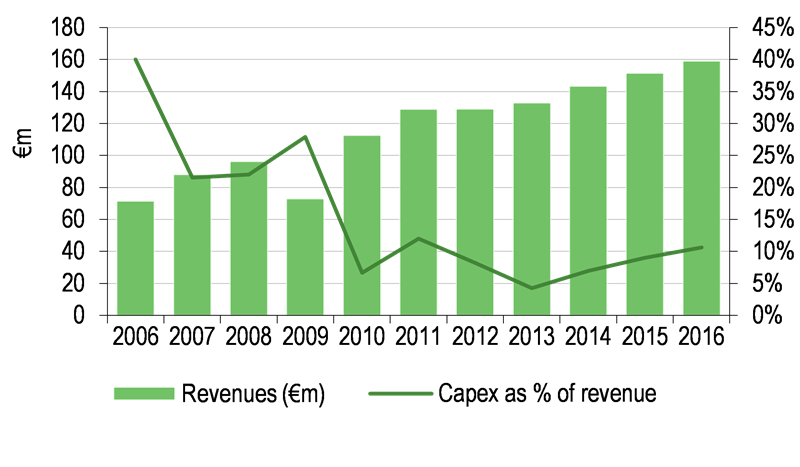
|
Source: Nabaltec accounts, Bloomberg consensus estimates
|
Source: Nabaltec accounts, Bloomberg consensus estimates
|
Exhibit 7: Revenue and margin progression
|
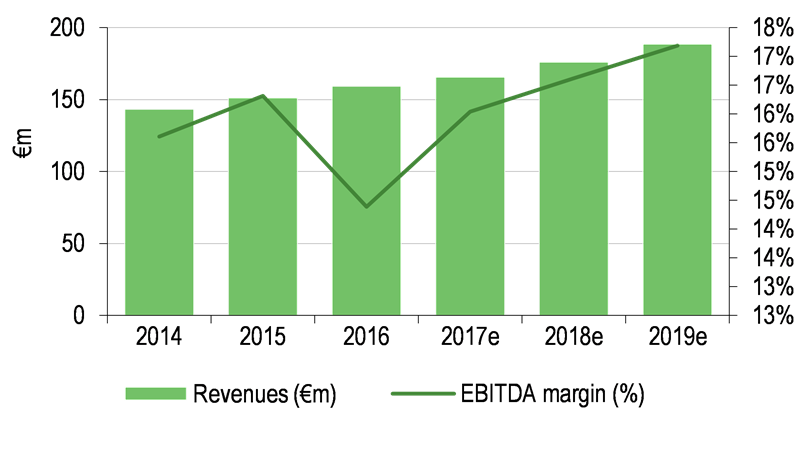
|
Source: Nabaltec accounts, Bloomberg consensus estimates
|
Exhibit 8: Revenue and capex development
|
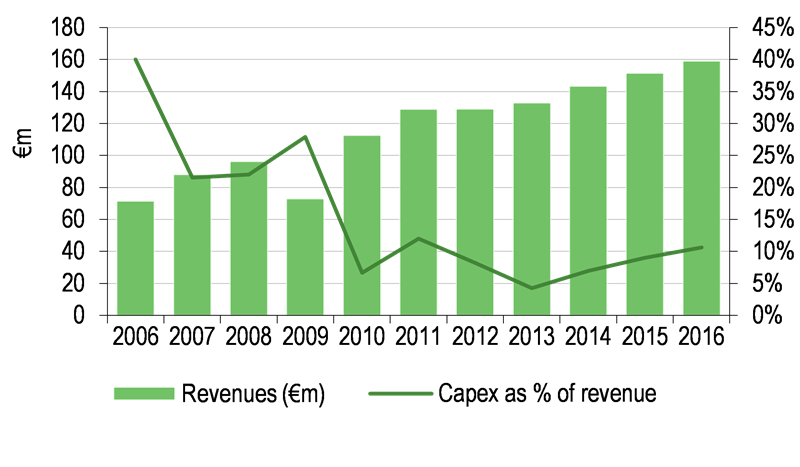
|
Source: Nabaltec accounts, Bloomberg consensus estimates
|
Total revenues rose by 5% (€7.9m) year-on-year during FY16 to €159.2m as both divisions showed modest growth. Revenues from Functional Fillers grew by 7% to €109.1m, driven by an increase in volumes. Boehmite revenues rose by 69%. Although boehmite does not represent a meaningful percentage of the total currently, this extremely strong growth indicates the potential for this new, high-margin product category. For the same period, revenues from Technical Ceramics increased by 2% to €50.1m, driven by volume growth, particularly in reactive alumina for longer-lasting refractories.
Cost of materials as a percentage of revenues reduced by 1.7pp to 50.7% because of a greater proportion of higher-value products and favourable gas prices during H216. Personnel costs increased by 18% (€4.9m) to €31.7m. This was partly due to an increase in the number of staff employed from 444 at end FY15 to 460 at end FY16, and partly due to a one-off non-cash item related to the impact of changes to the management board on pension reserves. Other operating expenses increased by €1.9m to €26.2m because of higher freight and other costs relating to the temporary closure of Nashtec, higher sales commissions and the expansion of sales activities in Asia and the US. EBIT margin fell by 1.8pp to 7.7%, EBIT by 16% (€2.3m) to €12.2m. Net interest payments fell by €0.6m, reflecting compete repayment of all bilateral loans, although this was partly offset by a €0.5m rise in income tax, which included a €0.8m adjustment in the losses carried forward associated with Nashtec. Management maintained DPS at €0.15, demonstrating its confidence that the dip in profits in FY16 is a one-off related to the temporary closure of Nashtec.
Balance sheet and cash flow
Net cash flow from operating activity was 30% higher in FY16 compared to FY15, even though EBIT was lower, because of favourable working capital movements. Net debt reduced by €4.9m during FY16 to €36.4m at the year end, cutting gearing from 71% to 63%. While gearing remains relatively high, it reflects the high levels of investment currently being made in the manufacturing facilities. The net total investment in FY16, which includes government grants, was €16.8m (FY15: €13.9m). Around three-quarters of the investment (€13.7m) was devoted to the Functional Fillers division for enhancing the production process, reducing energy consumption and increasing capacity for fine precipitated aluminium hydroxide. The €5.3m investment in the Technical Ceramics division was spent primarily on expanding capacity for high value-added products and optimising production processes. This level of investment is a relatively high proportion of the cash generated from operations (€22.9m net operating income before changes in working capital in FY16). However, it is necessary to provide sufficient capacity and to keep the product portfolio focused on growth niches, especially as new applications such as electric vehicles and renewable energy storage solutions are identified.