Central to Lepidico is its L-Max technology. L-Max is a hydrometallurgical process that uses readily available mainstream chemicals (eg sulphuric acid, lime and limestone) to extract and recover lithium from lithium containing micas. Lithium micas are abundant across the world, but are not typically treated owing to their having a lower lithium content than spodumene and conventional roast processing not affording the production of by-products (see below).
In crude terms, concentration of the micas ahead of the L-Max process occurs through simple rougher flotation at a fine grind size and with rapid flotation kinetics. Test-work, completed on various mica samples, has resulted in recoveries in the high 80%s to low 90%s. The mica concentrate is treated with sulphuric acid to dissolve the metallic ion salts and filtered to separate silicate by-products and to remove waste. The leach liquor is then subjected to a series of impurity removal and precipitation steps at different pH levels (sequentially, via the addition of limestone and lime) to produce a >99.8% Li2CO3 product that is typically sold to refiners on three- to five-year contracts for conversion into specific industrial salts and chemicals (eg lithium hydroxide, LiOH). A schematic representation of the L-Max process flowsheet is provided below:
Exhibit 2: Schematic representation of the L-Max process
|
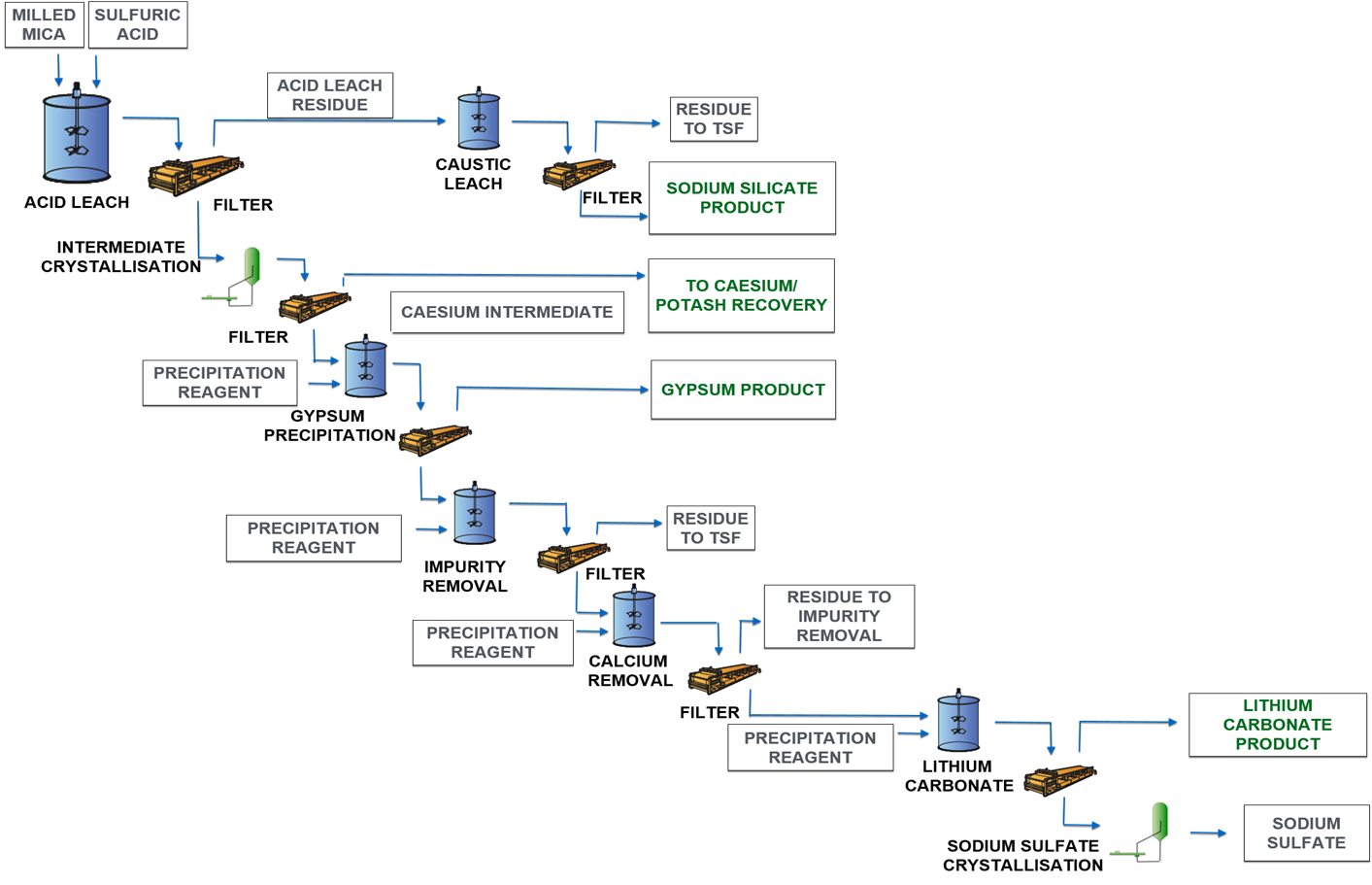
|
|
While the chemistry of the L-Max process is novel from an industrial perspective, it uses only common reagents and standard equipment. The process is conducted at atmospheric pressure and at temperatures that do not exceed 115°C. It produces little residue and the tailings are benign.
Significantly, in addition to lithium carbonate, the L-Max process can also produce a suite of valuable by-products, including sodium silicate (water glass), sulphate of potash (SOP), tantalum or tin (if present) concentrate, gypsum, and sodium sulphate. There is also potential to recover both caesium and rubidium into a formate solution. The former is in demand as drilling completion fluids in the oil and gas industries. Caesium, in particular, is a high value product. Typically, only the caesium content of the brine is valued. Sodium sulphate and gypsum are present in the process residue. Finally, when the leach residue is reacted with caustic soda, it produces sodium silicate solution. While relatively unknown to investors, sodium silicate has a multiplicity of industrial uses, including as a bulking agent, an additive to paints, adhesives (eg wallpaper paste), corrugated cardboard and fillers, as a fire retardant and as a precursor to precipitated silica in tyres. The market for sodium silicate, in particular, was instrumental in identifying Kenora as a potential site for the Phase 1 plant (see L-Max plant location on page 9, below). One imperative of the PFS (see page 8) was a requirement not only to minimise the costs of consumables (including logistics), but also to maximise the value of by-products. This dual requirement had the effect of disqualifying Australia as a potential site for the Phase 1 plant as a result of its not being a major producer of sulphuric acid nor having a deep market for silicates and other potential by-products.
Thus far, Lepidico has conducted large scale laboratory tests, at a feed rate of up to c 3kg per hour, that have shown the L-Max technology to operate continuously and stably over a protracted period of time. As such, Lepidico’s strategic imperative in proving the L-Max concept is now to scale the process up to approximately 3tph in a demonstration plant – the so-called Phase 1 plant considered in its PFS (see page 8). Ordinarily, such a plant would seek only to prove that it could operate from a technical perspective. In this particular case however, the company is confident that it will also operate from a commercial perspective – ie it will provide a positive return to shareholders. Although the process chemistry has proved itself to be robust in continuous mini-plant trials, inevitably, a period of time will be required to optimise the operation of the process (eg flow rates, leach times etc). Thereafter, however, a number of alternatives under its business model exist, by which Lepidico may commercialise its technology at full scale.
Lepidico’s favoured route to commercialisation is to leverage its technology to acquire control of quality lithium mica assets to form an integrated lithium producer (see Exhibit 3 on page 6). Currently, Lepidico has agreements over a number of prospective lithium mica exploration assets (see Geological assets, below) which could yield a resource in the order of 1Mt with as little as six weeks of additional drilling. Depending on grade, etc, a c 1Mt resource, of which 70% is convertible into reserves, would be capable of supporting the Phase 1 plant for approximately 10 years. That being the case and having completed a PFS on the Phase 1 plant, Lepidico is now only six to nine months from completing a feasibility study (FS) and then, potentially, as little as two years from profitable production.
Lepidico has also licensed its technology to other companies. Alignment of interests with licensees and the preservation of the reputation of its IP is supported by Lepidico having the right to review all technical data relating to a project prior to finalising a licence.
A schematic representation of Lepidico’s business model options is as follows:
Exhibit 3: Lepidico business model
|
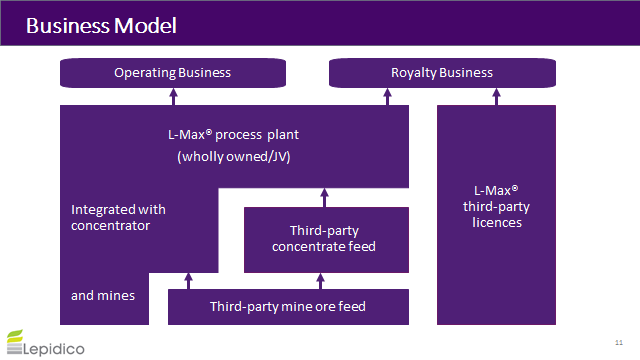
|
|
The two main sources of lithium in the world today are hard rock spodumene deposits and salar brines. Historically, commercial lithium production has been derived from hard rock mineral ore sources such as spodumene. Recently however, the development of salar brines from South America has expanded rapidly.
Global supply of lithium carbonate equivalent (LCE) is estimated to be in the order of 180ktpa, of which production of lithium via spodumene is c 80ktpa, primarily from pegmatites in Western Australia (of which Greenbushes is the largest and highest grade) and from some Chinese, Chilean and Argentinian brine sources. Output is dominated by six operations owned by four major companies (representing 91% of total market share), namely Albemarle, SQM, FMC and Sichuan Tianqi Lithium.
Recycling of lithium has also grown notably since Japan opened its first lithium-ion battery recycling plant in 1992. Facilities in Belgium, Germany, Japan, the US and Canada can all now process batteries for their lithium and other components.
Hard rock spodumene deposits occur in lithium rich pegmatites and aplites as colourless to yellowish, purplish or lilac kunzite or yellowish-green or emerald-green hiddenite crystals. The largest concentrations are found in granitic pegmatites (granite-like igneous rocks composed of quartz, feldspar and mica). The most important of these minerals are spodumene, which is a pyroxene mineral (LiAl(SiO3)2 or, alternatively, Li2O, Al2O3.4SiO2) and petalite (Li2O,Al2O3.8SiO2). Source localities include Afghanistan, Australia, Brazil, Madagascar, Pakistan, Quebec, North Carolina and California. Associated minerals include: quartz, albite, petalite, eucryptite, beryl and lepidolite (the focus of the L-Max process).
Theoretically, spodumene contains 8.03% Li2O and is usually recovered through conventional open-pit mining methods and beneficiated via gravity techniques, whereby the ore is concentrated from a 1-2% Li2O ore grade to a c 6-7% Li2O concentrate grade (ie 75-87% spodumene).
Pre-flotation treatment (ie cleaning) followed by oleic (fatty) acids or soap flotation and de-sliming is one well established recovery method for spodumene concentration. Alternatively, spodumene may be agitated with anionic collectors, followed by flotation. Oleic acids and soaps tend to produce a superior recovery in neutral and slightly alkaline pulps while napthanic acids, sulphonated castor oil, etc, tend to work better in an acid pulp.
In order to convert it to globally traded lithium carbonate, the concentrate is heated to over 1,100°C in a rotary kiln, before being crushed and treated with sulphuric acid. The resulting solution is first neutralised with limestone and then treated with soda ash (sodium carbonate) to produce a lithium carbonate solution. This solution is then evaporated prior to the addition of more soda ash to precipitate lithium carbonate.
Lithium brine deposits are formed via the leaching of volcanic rocks in basin depositional environments. Salar brines can be described as underground reservoirs that contain high concentrations of dissolved Group I metal salts, such as lithium, potassium, and sodium and are generally found below the surface of dried lakebeds (particularly in South America).
Lithium is extracted from brines via a process that involves pumping the brine from the sediment basin and then concentrating it via solar evaporation over a number of months or even years. Potassium is often harvested first from early ponds, while later ponds have increasingly high concentrations of lithium. When the lithium chloride in the evaporation ponds reaches an optimum concentration, the solution is pumped to a recovery plant where filtering removes any unwanted boron and/or magnesium. Purification then occurs via solvent extraction, absorption and ionic exchange with sodium carbonate (soda ash) to precipitate refined lithium carbonate (Li2CO3). Alternatively, lithium chloride is a convenient intermediate salt from which to directly produce lithium hydroxide. Finally, excess residual brines are then pumped back into the salar. Since salar brines naturally occur at high altitudes and in areas of low rainfall, solar evaporation is a very efficient method for precipitating salts and it has been estimated that the cost of extracting lithium from such sources may be half of that from hard rock sources.
Advantages of spodumene processing
Notwithstanding their typically higher cost structure, pegmatite-based projects benefit from being quicker to move into production than brines, which may have a lead time of 1.5-3 years from the start of commercial extraction, depending on evaporation rates. Another key advantage of lithium production from hard rock deposits is the purity of the lithium carbonate produced. While the battery industry requires a minimum purity of at least 99.5% lithium carbonate, the composition of the remaining 0.5% is important and commercial penalties are often imposed for lithium carbonate containing enhanced levels of deleterious elements, such as iron, magnesium, etc.
Disadvantages of spodumene processing
In contrast with salar brine sources (see above), recovery of lithium from hard rock deposits, such as spodumene, requires a wide range of hydro-metallurgical processes. Pegmatite ores containing spodumene always contain other minerals such as mica, feldspar and quartz and iron and other silicates that have a tendency to concentrate with the spodumene. Problems associated with spodumene recovery therefore include the degree to which weathering has occurred and the presence of associated gangue minerals. Weathered mineral surfaces must be thoroughly cleaned before selective flotation. In addition, weathering and surface oxidation of the rocks may also give rise to alteration products that interfere with the flotation process. Gangue minerals may interfere with selective flotation, as well as consuming process reagents.
Lepidolite as an alternative source of lithium to spodumene
Lepidolite is a lilac-grey or rose-coloured member of the mica group of minerals with the formula K(Li,Al)3(Al,Si,Rb)4O10(F,OH)2. It is a phyllosilicate mineral and a member of the polylithionite-trilithionite series. Compared to spodumene’s 8.03%, lepidolite theoretically contains 7.70% Li2O. Despite being an abundant lithium-bearing mineral, to date it is only a secondary source of the metal, with only a few, small-scale producers in the western world exploiting lepidolite purely for use in the ceramics industry. Otherwise, it is also produced in China as a precursor to the production of lithium – albeit via a commercially inefficient roasting process. Consequently, there has been little or no global exploration for lithium-bearing micas, with the result that the best potential assets remain un-investigated, even at surface. Notable occurrences have been reported in Brazil, the Ural Mountains, California, Manitoba (the Tanco mine – an underground caesium and tantalum mine, owned and operated by Cabot Corporation, which is the world’s largest producer of caesium), Madagascar, the Iberian Peninsula and Zimbabwe.
Zinnwaldite was first described in 1845 in Zinnwald (Cinovec) on the German-Czech border and is a silicate mineral also in the mica group. Chemically, it may be described as potassium lithium iron aluminium silicate hydroxide fluoride with formula KLiFeAl(AlSi3)O10(OH,F)2. It occurs in greisens, pegmatite, and quartz veins often associated with tin ore deposits and is commonly associated with topaz, cassiterite, wolframite, lepidolite, spodumene, beryl, tourmaline and fluorite. Compared to spodumene’s 8.03% and lepidolite’s 7.70%, zinnwaldite theoretically contains 3.42% Li2O.
Other sources of lithium, to which Lepidico’s L-Max technology may prove to be applicable, include amblygonite (7.4% Li2O).