Kinsevere – located in Congo mining province
We recently had a site visit to Kinsevere copper mine and consequently make this the focus of this note. We have, meanwhile, updated our group forecasts to take account of recently published 2015 results, commodity and exchange rate movements, and company guidance for 2016 production and costs. In 2015 the Kinsevere mine reported record production, reduced costs, and accounted for around one-fifth of group revenues and 21% of EBITDA from operations.
The Kinsevere copper mine (MMG 100%) is approximately 30km north-east of the city of Lubumbashi in the Katanga province, DRC. Katanga province is located in the south-east corner of the DRC.
MMG acquired its interest in Kinsevere through a friendly C$1.3bn takeover offer for Anvil Mining in 2011 and the acquisition of the remaining 5% minority interest from MCK, a local mining contractor, in 2012.
At acquisition, the nameplate capacity of the Kinsevere plant was 60,000 tonnes per annum cathode. As a result of a wide range of initiatives, the site has increased copper production to over the 80,000 tonnes per annum cathode level without major capital expenditure.
The greater scale of the operation plus direct cost initiatives has led to a reduction in costs. C1 cash costs used to be around the US$1.80/lb cathode level. From this level, C1 costs have been consistently falling. The C1 cash cost guidance for 2015 was US$1.50-1.70/lb copper cathode. The actual achieved C1 cost for 2015 was US$1.48/lb. The company’s C1 cost guidance range for 2016 is US$1.40-1.55/lb copper cathode.
Exhibit 1: Location of Kinsevere mine, Democratic Republic of the Congo
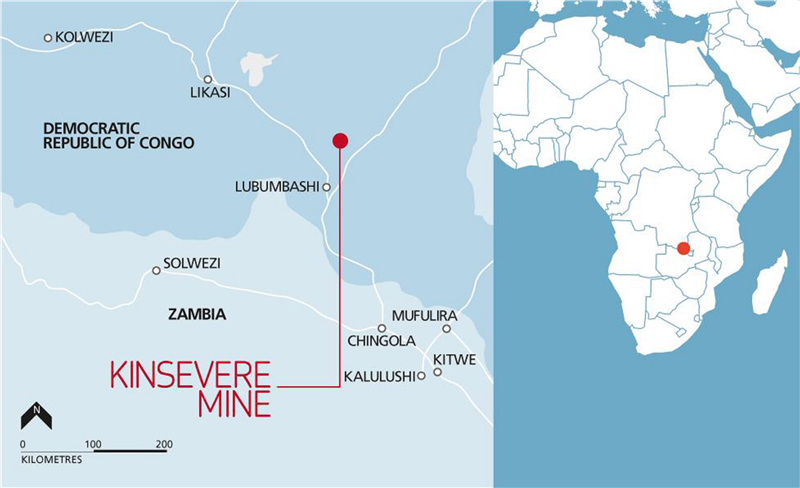
Kinsevere integrated into the MMG ‘central hub’ model
As part of a company-wide strategy to minimise costs, MMG’s ‘central hub’ model has recently been implemented at Kinsevere. This seeks to achieve synergies and efficiencies through the global centralisation of administrative functions such as finance, payroll, accounts and human resources. The model is supported by site-based SAP systems.
With the centralisation of non-core functions, site staff are able to have greater focus on site-based activities such as safety, production volumes and operating costs.
Mining operations: Open-pit mining, high copper grades
Mining operations are conducted by open-pit methods. The ores mined are the oxide types malachite and cuprite with a small proportion of transitional ore and minor native copper. The current life of mine (LOM) is out to 2024 after taking into account mining from oxide resources and recovery from existing oxide stockpiles.
The mining rate is designed to feed the 2.3Mtpa processing plant with ore blending to produce a copper feed grade of around 3.7%. Depending on the mining sequence, the mining rate may differ from the processing rate due to stockpile build or withdrawal. Typical working stockpile inventory is 100,000 tonnes. Kinsevere also maintains a much higher stockpile balance of 4.8mt at 2.1% copper (Exhibit 4), partly to manage Run of Mine (ROM) head grade and partly for stockpiling low-grade ore for processing later in the mine life. Currently, all mining is from the Central pit, but the future mine plan calls for two or three pits to be mined concurrently. The total life of mine waste to ore ratio is 2:1. The approximate mining sequence is as follows, with:
■
Central (Tshifufia) pit – Stage 3 (current depth 90m) to be mined until October 2016 with Stage 4 being mined to a total depth of approximately 140m from February 2017 to May 2020. The Central pit has bench heights and berm widths of 10m and 6m respectively and an average effective slope of 45 degrees.
■
Kinsevere Hill North pit – to be mined from August 2016 to May 2017.
■
Mashi (Tshifufiamashi) pit – mining from March 2017 to September 2019.
■
Kinsevere Hill South pit – mining from November to March 2021.
Exhibit 2: Kinsevere mine overview
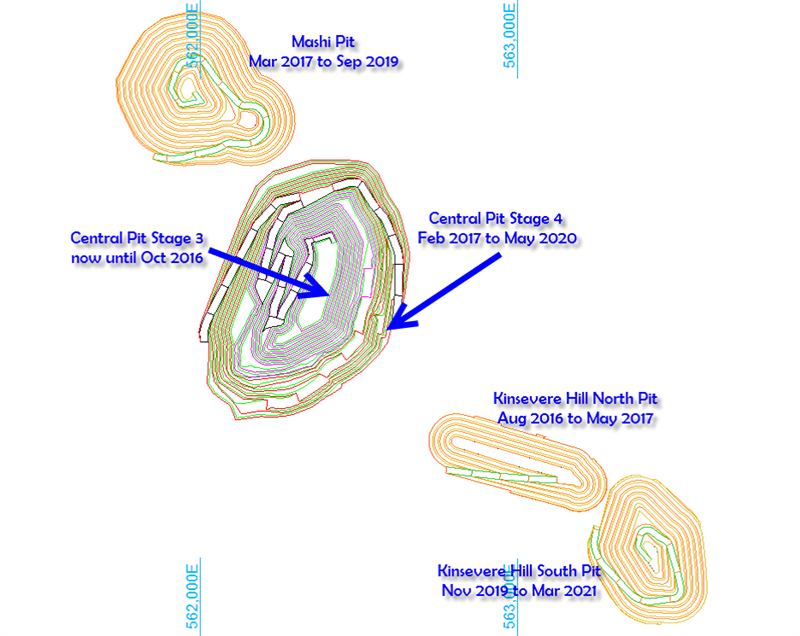
MMG employs the contractor MCK for most mining functions at Kinsevere including civil works, mine development and drilling. Ore and waste haulage is by six-wheel articulated trucks with a capacity of 15-16m3 (approximately 40 tonnes). These trucks are small for a mining operation and are more commonly employed in civil applications. However, they are very suitable for wet weather conditions and provide good operating flexibility. The wet season extends from October to April, with the wettest periods in January and February. Kinsevere continues to focus on initiatives that will lead to further mining efficiencies.
Mine planning and blast drillhole planning is carried out by MMG staff. Loading of the drill holes with explosive emulsions is carried out under a service contract by explosives manufacturer AEL.
Within the DRC copper belt, a number of different mining contractors are active.
Ore processing – emphasis on maximising refining capacity
Kinsevere mines and processes oxide ore. This enables the operation to use the conventional solvent extraction/electrowinning (SXEW) process (Exhibit 3) to produce A grade refined 99.99% copper cathode. Achieved capacity is just above the 80,000 tonnes per annum level.
Factors behind achieving this level of capacity (against a 60,000 tonnes per annum nameplate) include maintaining continuous power availability and a very strong emphasis on the continuous cleaning and maintenance of busbars and cathodes in the refining house. This has enabled the cells to operate at a high current density without loss of current efficiency.
With minor capital expenditure, MMG believes it can ultimately lift refining capacity above the current 80,000tpa rate.
The Kinsevere operation was commissioned in 2007 as a Heavy Media Separation (HMS) operation with a copper concentrate product. The current SXEW plant was completed in 2011 and the HMS plant was closed.
Elements of the current plant and SXEW process include:
■
Mineral sizer – this breaks up the rock prior to the semi autogenous grinding (SAG) mill.
■
Ore grinding – this uses a single stage SAG mill operating in a closed circuit. This produces a 200 micron feed, which is then directed to the leach tanks. The SAG mill operation is unusual in that sulphuric acid is added to the circuit to start the leach process early in advance of the leach tanks. The leaching process involves the extraction of copper from solid copper oxide using the sulphuric acid solution. Although the acid concentration in the SAG mill circuit is lower than that in the leach tanks, it is very effective because of the high kinetic energy in the SAG mill. The SAG mill has a mild steel shell with an epoxy coating on the inside to prevent acid erosion. The mill is topped up with concentrated acid as necessary.
Leaching of copper from the ore into solution
The objective is to dissolve the copper into solution. This is upgraded and clarified to produce a pregnant leach solution (PLS):
■
Leach tanks – these are atmospheric agitated leach tanks. The residence time in the tanks is six hours. The leached slurry, which contains both copper in solution and un-dissolved copper in solids, passes to the high-grade thickener.
■
High-grade thickener – Overflow from the thickener containing copper in solution, mainly as copper sulphate, passes to a high-grade pinned bed clarifier for further upgrading. Slurry underflow from the thickener, which contains copper not yet dissolved, passes to the counter current decantation (CCD) circuit.
■
High-grade pinned bed clarifier – this removes remaining solids and produces a clarified high-grade pregnant leach solution (PLS), which is the feed for the high-grade circuit of the solvent extraction (SX) process. Underflow from the clarifier is recycled back to the thickener.
■
CCD circuit – Slurry underflow from the thickener is pumped sequentially through five CCD thickeners in series. The slurry underflow liquor is diluted with wash liquor that flows in the opposite direction. The wash liquor leaches out most of the remaining copper in solids and forms the low-grade PLS. After clarification in a low-grade pinned bed clarifier, the clarified low-grade PLS solution provides the feed for the low-grade circuit of the solvent extraction circuit.
Exhibit 3: Kinsevere copper processing plant (milling, leaching, SXEW)
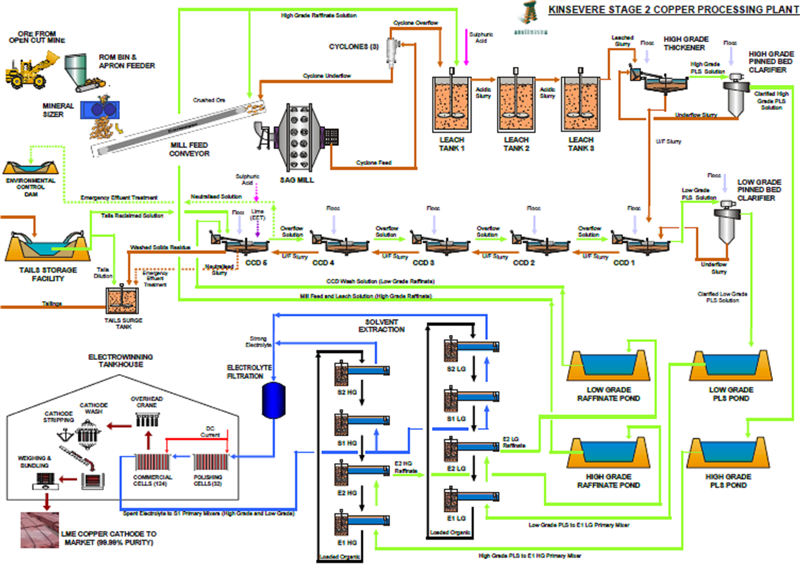
Solvent extraction is the method used to purify the copper solution for copper refining.
At Kinsevere, there are two SX trains comprising a low-grade circuit (for the low-grade PLS) and a high-grade circuit (for the high-grade PLS). This configuration has the advantage of improving copper recoveries and reducing acid consumption.
■
The SX process uses mixing and settling tanks to contact the pregnant acidic liquor with an organic solvent. The copper is extracted away from the aqueous phase into the organic phase, leaving most of the impurities behind.
■
The copper bearing organic phase is then contacted with a strongly acidified aqueous solution. This causes the copper to move to the aqueous phase while the organic phase is reconstituted in its hydrogen form. The density difference between the aqueous solution and the organic solvent is used to separate the two solutions after the copper has been transferred.
■
The copper bearing aqueous phase is then advanced to the electrowinning stage, while the organic phase, now devoid of copper, is returned to the extraction stage. The spent impure acid solution or raffinate is recycled back to the SAG mill, leach tank and CCD circuits.
In the EW process, the copper is reduced electrochemically from copper sulphate in solution and is deposited as copper metal onto a stainless steel sheet, which acts as a cathode.
■
Electrowon copper cathodes are as pure as or purer than electrorefined cathodes from traditional smelting processes.
■
Kinsevere has two tank houses. The EW cells run at a very high current density. Kinsevere claims the very high current density used at the refinery is the second highest in the world. Despite the high current density, the current efficiency of 91% does not appear to have fallen.
■
When the copper deposited has achieved the desired weight, a crane is used to remove the copper cathode from the electrolytic cell. The copper is then stripped from the stainless steel cathode in an automated process. The copper cathodes are then bundled and weighed, ready for shipping.
■
A methodical anode and cathode maintenance and cleaning regime is in place to achieve maximum current efficiencies.
Tailings Storage Facility (TSF)
This is for the storage of all acidic tailings from the process.
■
The current facility is designed for Life of Mine (LOM) requirements and has a footprint for expansion. Acid liquor is recycled with water top up to make up for evaporation.
There is a heap leach facility, which is now in a dormant stage. Kinsevere may look at some form of heap leach operation for the future, potentially to treat ore from additional sources, particularly low-grade material.
An advantage of a heap leach facility is its low capital cost and operating flexibility.
Power – continuity of supply crucial for copper refining
Power is supplied to Kinsevere by Société Nationale d'Electricité (SNEL), the national electricity company of the DRC, and other external suppliers including Copperbelt Electricity Corporation (CEC) and Zesco of Zambia. However, historically, power supply proved to be unreliable, with occasional blackouts.
Due to the instability of grid power, 24 diesel powered generator sets were installed on site in 2012/13 to supplement power from SNEL. These gave 17MW power.
Negotiations were also conducted with other external power suppliers to provide additional power security. In addition, further site generators were added to bring the total of on-site generators to 31 generators, equivalent to 24MW and potentially up to 28MW. This means the site can be self-sufficient during periods when grid power is not available.
In 2011, only 63% of power requirement was able to be supplied from grid source power providers. This increased to 74% in 2015 and 90% in the month of December 2015. This is a substantial improvement and reflects a lot of work and engagement between Kinsevere and external power providers.
The current strategy is to run three to four generators at a time to provide a ‘spinning capacity’ of 2MW, which ensures the site does not have a blackout. Additional site generation can be spooled in after 2-2.5 minutes in the event of grid power issues. This allows the operation to maintain consistent operation.
Logistics and port access – further progress expected
The location of the Kinsevere mine is logistically challenging. This increases the costs of imported consumables used in copper production and increases waiting times and working capital. A lot of work has already been carried out to reduce logistics costs, which are regarded as too high. Kinsevere would like to see a greater local content in the consumables it is able to buy. Most of the sulphuric acid it uses is imported from Zambia and is derived from smelter flue gas.
Current and potential future port facilities are:
■
Dar Es Salem – copper cathode is currently exported by road to the port of Dar Es Salem, Tanzania, for export. This is expensive.
■
Angola – Initiatives are underway to rehabilitate the multi-modal Lobito Corridor from Lobito on the Atlantic Coast in Angola to Lubumbashi in the DRC. This includes the Benguela Railway and various ports, roads, airports and logistics platforms. This corridor used to be the main export route for copper from the DRC and Zambia but was abandoned due to the civil war in Angola in the 1990s.
■
Namibia – There is an existing deepwater port at Walvis Bay, Namibia, which has the potential for the future export of copper cathode and import of consumables.
Oxide reserves and resources
Kinsevere has oxide reserves and stockpiles (Exhibit 4) that are sufficient for LOM operations to 2024.
Exhibit 4: Kinsevere oxide reserves at 30 June 2015
|
Oxide copper (Mt) |
Cu (%) |
|
Stockpiles (Mt) |
Cu (%) |
|
Total (Mt) |
Cu (%) |
Proved |
2.9 |
4.7 |
|
1.4 |
3.7 |
|
4.3 |
4.4 |
Probable |
6.6 |
3.9 |
|
3.4 |
1.4 |
|
9.0 |
3.2 |
|
|
|
|
|
|
|
|
|
Total |
9.4 |
4.1 |
|
4.8 |
2.1 |
|
13.2 |
3.5 |
Oxide resources (Exhibit 5), which are inclusive of reserves, may provide the potential for additional operations life, subject to conversion to reserves.
Exhibit 5: Kinsevere oxide resources at 30 June 2015
|
Oxide copper (Mt) |
Cu (%) |
|
Stockpiles (Mt) |
Cu (%) |
|
Total (Mt) |
Cu (%) |
Measured |
3.7 |
4.5 |
|
6.4 |
2.3 |
|
10.1 |
3.1 |
Indicated |
11.9 |
3.4 |
|
|
|
|
11.9 |
3.4 |
Inferred |
4.2 |
3.3 |
|
|
|
|
4.2 |
3.3 |
|
|
|
|
|
|
|
|
|
Total |
19.8 |
3.6 |
|
6.4 |
2.3 |
|
26.2 |
3.3 |
Kinsevere primary resources
Primary sulphide resources (Exhibit 6) underlie the oxide resources at Kinsevere. MMG believes sulphide resources have the potential to extend the mine life at Kinsevere to 2033, which would increase operations life by approximately 10 years.
MMG is currently conducting a pre-feasibility study (PFS) for the development of Kinsevere’s sulphide resources. Additional processing would be required, which could involve the production of sulphide concentrates.
Exhibit 6: Kinsevere sulphide resources at 30 June 2015
|
Primary copper (Mt) |
Cu (%) |
|
Stockpiles (Mt) |
Cu (%) |
|
Total (Mt) |
Cu (%) |
Measured |
1.6 |
3.2 |
|
0.0 |
0.0 |
|
1.6 |
3.2 |
Indicated |
10.9 |
2.2 |
|
|
|
|
10.9 |
2.2 |
Inferred |
14.6 |
2.4 |
|
|
|
|
14.6 |
2.4 |
|
|
|
|
|
|
|
|
|
Total |
27.1 |
2.3 |
|
0.0 |
0.0 |
|
27.1 |
2.3 |
Exploration in the globally significant DRC copper belt
The Katanga copper belt in the DRC contains some of the highest-grade copper deposits in the world. It is formed in the rocks of the Katanga Supergroup, which is about 70km wide and 250km long between Lubumbashi and Kolwezi. The region is host to significant stratabound sediment hosted carbonate rich copper deposits. These deposits are normally processed using SX/EW methods.
The DRC is the world’s fifth largest copper producer with annual production of approximately 1Mtpa copper metal. MMG has a strong commitment to exploration, with exploration expenditure of US$73.0m in CY14 and US$42.4m in CY15. A large percentage of the company’s exploration budget is spent in the DRC.
MMG’s expenditure in the DRC is mainly directed towards increasing resources that can be processed through the Kinsevere mine infrastructure. Its focus is the Rad50 project, which targets potential discoveries within a 50km radius of the Kinsevere mine. The project includes exploration and mining rights over 15 tenements adjacent to the Kinsevere operation, which were acquired in 2013.
MMG’s near-term goal is to discover the equivalent of at least one Kinsevere size resource to extend the life of the existing infrastructure.
Kinsevere is currently looking at opportunities to purchase copper ore from the owners of copper resources that do not have processing facilities.
Heap leaching may provide a more flexible and lower capital cost processing route for potential copper ore purchases. There is potential to increase Kinsevere’s copper refining capacity to above the current 80,000 tonnes per annum rate, at low capital cost, to accommodate purchases.