BCI’s key mining projects
Mardie Salt and SOP project
The Mardie project is located on the West Pilbara coast, between Dampier (95km north-east of Mardie) and Onslow (90km south-west of Mardie), which is Australia’s major solar salt production and export region, including operations such as Rio Tinto’s Dampier Salt (the world’s largest single salt exporter). BCI intends to develop the project into a long-life operation, producing both salt and SOP via the solar evaporation of seawater.
Exhibit 3: Mardie salt project location
|
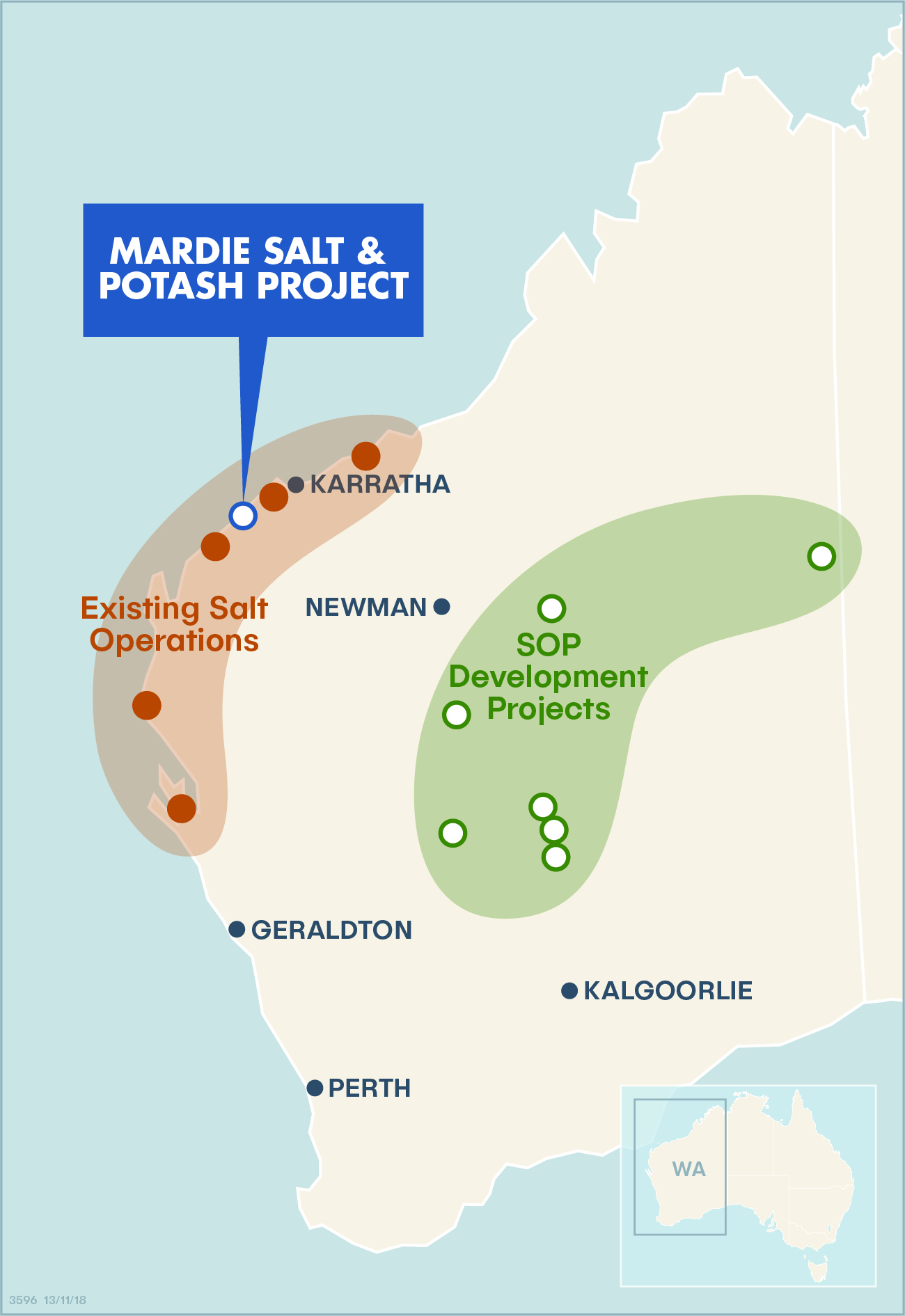
|
|
The region is favourable for oceanic salt extraction operations because of its access to natural channels that feed seawater to the project area and a low-permeability, flat landscape that is suitable for constructing evaporation ponds. The region’s windy, hot and dry climate is classified as ‘grassland’ by the Bureau of Meteorology, which means it experiences hot weather throughout the year with a summer drought. The Mardie tenements, in particular, comprise extremely flat mudflat topographies behind the coastal mangroves. The project has five granted exploration licences and one exploration licence application, encompassing a total area of 912km2.
A scoping study released in July 2017 by BCI demonstrated positive results for developing a 3–3.5Mtpa operation to produce high-purity, industrial-grade sodium chloride salt from seawater for onward sale to the chlor-alkali industry. The study assessed a 20-year mine life, although the project could potentially operate (effectively) almost indefinitely, given that the input resource is seawater. Capital expenditure was estimated at A$225–255m with an accuracy of ±35%. Operating costs were expected to be c A$19–21/t on a free-on-board (FOB) basis, which generated a pre-tax NPV of A$290–380m over a 20-year life at a 10% discount rate and a pre-tax IRR of 25–27%. The study assumed the export of salt via the Cape Preston East Port. In due course, it was observed that Mardie could also benefit from synergies with BCI’s Carnegie project, which has a similar pond design principle and processing and marketing dynamics.
The results of the Mardie PFS were announced in June 2018. As per the July 2017 scoping study, the ultimate aim of the project was presumed to be the production of 3.5Mtpa of high-purity, industrial-grade sodium chloride salt and 75ktpa of SOP from seawater via solar evaporation, crystallisation and purification. The salt was then presumed to be exported via a purpose-built transhipping operation at BCI’s planned Cape Preston East Port (note: SOP, see below, was presumed to be exported from the existing general cargo wharf at Port Dampier). The study was conducted in conjunction with at least 18 external consultants, including Salt Partners, Roskill and Braemar Shipping Services, with the objective of improving the scoping study design footprint, reducing technical and approval risks and evaluating the viability of a SOP processing flowsheet in addition to the salt one. A range of field studies, sampling and test-work programmes and surveys were undertaken regionally and locally to define the project design criteria and operational and capital cost estimates were undertaken to an accuracy of -15% to +25%, qualifying it as equal to, or better than, an AACE Class 4 estimate, as defined under Association for the Advancement of Cost Engineering Recommended Practice Number 18R-97 (ie a pre-feasibility study).
Geotechnical and hydrogeological
The Mardie site has all the natural hydrological, climatic, topographical and geotechnical prerequisites for the production of salt and SOP from solar evaporation. In addition, it is also ideally situated to access Asia’s key growth markets.
Critical geotechnical requirements for the construction of 89km2 of concentrator and crystalliser ponds are:
■
The presence of a low permeability clay layer that extends across the proposed pond footprint in order to reduce product losses via seepage and eliminate the need for pond liner.
■
The availability of material suitable for constructing low-permeability walls in order to eliminate the need to source and transport suitable materials to site.
The tests conducted in the context of the PFS have allowed BCI to conclude that a low-permeability layer is extensive across the proposed pond footprint and that construction materials for the pond walls are available.
Similarly, hydrogeological studies have concluded that:
■
Surface water flows from land to sea are minimal and, such as they are, may be accommodated by three sets of diversion bunds and three diversion channels through the project area to ensure that water flows are managed effectively, without affecting ponds or project infrastructure.
■
The project is protected from potentially damaging sea to land water movements (eg storm or cyclone-induced surges and waves) by two lines of defence, namely the island archipelago system directly adjacent to the coast and the mangrove swamps lining the coast, and the fact that the ponds will be located 2–3km inland.
Sodium chloride salt
A seawater pump will extract 132 billion litres (132 x 109 litres or 132Gl – approximately 135.8Mt) of seawater, containing c 5.4Mt of salts (containing c 4.2Mt of sodium chloride and 135kt of SOP equivalent) per year and transfer it to the first of eight concentrator ponds. The seawater will then progress from Pond 1 to Pond 8 over a period of approximately one year (similar to lithium salt extraction from the South American salars), at which point solar evaporation will have reduced it to 12% of its original volume and its specific gravity will have increased to 1.216g/cm3 (ie close to the point of salt crystallisation). From Pond 8, 18Gl of concentrated seawater (augmented by a recycled stream from the SOP production circuit) containing 4.8Mt of sodium chloride per year will be deposited into a series of 12 crystalliser ponds, from where 3.8Mtpa of raw salt will be crystallised at specific gravities of 1.227–1.250g/cm3. At a specific gravity of 1.250g/cm3, the crystallisers are drained and raw sodium chloride salt is dry harvested for treatment in the salt purification plant. The bitterns drained from the crystallisers total 6.0Gl per year and contain 1.0Mt of residual sodium chloride salt and 130kt of SOP equivalent (see below). The dry harvested salt is then hauled to a 700tph purification plant, designed by Salt Partners, using its proprietary HYDROSAL-XP salt purification process to minimise product losses (c 2–3% cf 20% via traditional methods) and maximise contaminant rejection to result in a high product purity of 99.7% on a dry basis. Finally, product is stockpiled at Mardie for up to six months to assist in dewatering and product quality. Total product losses of 7% have been assumed in the study, from harvesting to export, to result in annual saleable production of 3.5Mtpa (note that the DFS is aiming to increase this by 14.3% to 4.0Mtpa).
SOP
The 6.0Gl of bitterns containing 1.0Mt of sodium chloride salt and 130ktpa of SOP equivalent (see above) is pumped to four parallel streams of nine sequential secondary crystallisers. The first four of the nine crystallisers will be primarily employed in precipitating mainly sodium chloride salt (albeit with sufficient contaminants to make it unsuitable for immediate purification), which is then re-dissolved in seawater before being returned to Concentrator Pond 7 (see above). Crystallisers 5 and 6 will crystallise a mixed salt with a low potassium content that is considered waste. Kainite-type mixed salts will then form in Crystallisers 7 and 8, with the final Crystalliser 9 being allowed to hold surplus liquor. The Kainite-type mixed salts are then dry harvested from each crystalliser and hauled to the stockyard and stockpiled separately, whence they are blended to provide a consistent feed for the SOP plant. The SOP plant crushes, screens and re-dissolves the Kainite-type mixed salts and subjects them to a solid/liquid separation process to remove the majority of the sodium chloride (which is returned to the crystallisers) to form a Schoenite mother liquor, which then proceeds to decomposition, washing, concentration and drying to become SOP product at a rate of 75ktpa for the purposes of the PFS, but potentially up to 100ktpa, with less conservative recovery assumptions, which is the aim of the DFS currently underway. SOP destined for overseas markets will then be bulk packaged on site and trucked to the general cargo wharf at Port Dampier for export in sea containers. Sales into the domestic Australian market will occur via road transport and/or coastal shipping.
Waste disposal
Waste, primarily in the form of bitterns and low potassium mixed salts from Crystallisers 5 and 6, will be transferred to a holding pond for dilution in seawater, prior to pumping via pipeline over the tidal flats into deeper water, where the waste liquid will be released through a purpose-designed diffuser.
The PFS assumed that the proposed Cape Preston East Port (CPE) will be constructed by BCI subsidiary, Cape Preston Logistics Pty (CPL) and will be expanded for salt export in addition to iron ore export. Within this context, product stockpiles at Mardie were presumed to be connected to CPE via a 19km sealed private project access road, which connects with a 48km section of BCI’s proposed sealed private road. However, management is also pursuing government support for the development of an export jetty at Mardie as an alternative to trucking salt c 70km to CPE. Internally, management expects this initiative to reduce opex costs by c A$4/t (or c 20%) as a result of eliminating haulage, operational simplifications and less process duplication, albeit at the expense of a c A$65m increase in capex. We understand the Mardie export jetty solution will form the basis of the DFS. The economic consequences of such an initiative are considered in the sensitivities section, on pages 20–22, below.
Critical ancillary infrastructure for the development of the project may be summarised as follows:
■
A 26km site access road.
■
Prefabricated, modular administration facilities.
■
Maintenance workshops (also serving as cyclone protection).
■
A village, comprising a nominal 100 accommodation units, mess etc and supporting central infrastructure (eg waste water treatment plant, communications etc).
■
A precast, concrete boat launching ramp.
■
Local diesel generation for the seawater pump station.
■
Mobile fleet, including raw salt harvesters, graders, raw salt haul trucks and product loading equipment.
■
A desalination plant to provide fresh process and drinking water.
■
A fenced landfill site.
The project has a five-year development timeline, from the completion of the PFS to first salt production in 2023. BCI plans to optimise the development timeline during the BFS and also to investigate opportunities to accelerate the schedule. To date, however, the project is planned to occur on a ‘just-in-time’ basis, commencing in early 2020. Key scheduled milestones are as follows:
■
April 2020 to October 2021: concentration ponds completed and transferred into service.
■
June 2021: first primary crystallisers ready for service and nominal 400mm salt floors to be prepared over the following 12–18 months to December 2022, before the first raw salt harvest six months later in June 2023.
■
H2 CY23: Completion of the salt purification plant.
■
2023: Secondary crystallisers for SOP production constructed and salt floors prepared over the following year, ready for feed into the SOP plant in H1 CY25.
Environmental and permitting
Key features of the Mardie project are that it is set back from the coast, thereby avoiding coastal vegetation as well as affording protection from cyclone-induced storm surges. The final environmental surveys relating to the project are currently underway. During the course of the Mardie PFS, at least 14 environmental studies were conducted, which resulted in the following modifications to the project compared with its original scope:
■
A substantial reduction in the size of the project area via the surrender of a tenement to avoid mangroves in the Robe River delta.
■
A further 3,000 hectare (29%) reduction in the project area to avoid algal mats.
■
Minimisation of clearing, dredging and other maritime disturbance.
■
Relocation of the western pond walls landward, with a 300m buffer between these walls and the mangrove algal mats, in order to minimise direct and secondary, indirect effects on the ecosystem.
■
Relocation of the western pond walls to allow algal mats to migrate landwards towards the seawall and along corridors in response to predicted sea level rises over the life of the project.
■
Installation of drainage corridors, designed to maintain hinterland and tidal creek flows (as much of nutrients as water) and connectivity.
Otherwise, a number of approvals will be required from a range of both State and Federal government departments, including the Department of the Environment & Energy (DOTEE), the Department of Water & Environmental Regulation (DWER), the Department of Mines, Industry Regulation & Safety and the Department of Planning, Lands & Heritage. Significantly, during the December 2018 quarter, the Environmental Protection Authority (EPA) approved the Mardie project’s environmental scoping document, which sets out the scope and content of the environmental review document (ERD) required to be submitted as part of the approval process. On the basis that the ERD is submitted by April 2019, the EPA endorsed a timeline whereby the EPA’s assessment report is released by the end of 2019, allowing full Ministerial approval by early 2020.
The licences comprising the Mardie project are covered by the claim areas of the Yaburara Mardudhunera and Kuruma Marthudunera native title claim groups. BCI has longstanding and strong relationships with both groups and existing land access deeds. In addition, it has completed a detailed heritage survey during the course of its PFS, in order to ensure the minimum disruption of sacred sites.
During the December 2018 quarter, BCI completed a positive heritage survey with the Yaburara and Mardudhunera people that covers approximately 90% of the project footprint. The result of the survey is that BCI has now received the required heritage-related consents to proceed with construction and operation activity in these areas, subject to relocation of some artefacts and preservation of a heritage site, which does not affect the planned project footprint. The company plans to complete a further heritage survey with the Kuruma Marthudunera people in the March 2019 quarter to cover the remaining 10% of the project’s footprint area.
Mardie has four important competitive advantages over its rivals:
■
A key barrier to entry for all solar evaporation salt projects is location. In this particular case, Mardie has secured a rare combination of a low-permeability, flat landscape in a hot and dry climate, close to existing infrastructure.
■
Current cost estimates derived from the pre-feasibility study suggest that, including SOP as a by-product, Mardie will be at the bottom of the global cost curve for salt production.
■
On the coast of Western Australia, Mardie is projected to have a US$15/t freight cost advantage over Mexico (the world’s eighth largest producer) in shipping to Asia.
■
Mardie will have a competitive advantage over domestic SOP producers that are typically located 800–1,000km from ports.
Iron Valley is an operating mine located in the Central Pilbara region that has been in production since October 2014. It has a relatively simple deposit geometry with a low waste to ore stripping ratio and produces both lump and fines that are transported to Port Hedland by trains and exported via Utah Point. At June 2018, it had reserves and resources capable of supporting a simple direct shipment operation with a life of c 13 years at current production rates of c 7.5Mtpa.
Exhibit 4: Iron Valley mineral resource estimate
Classification |
Cut-off (% Fe) |
Mt |
Fe (%) |
Ca Fe (%) |
AI2O2 (%) |
SiO2 (%) |
P (%) |
LOI (%) |
Measured |
50 |
92.0 |
57.8 |
62.6 |
3.2 |
5.4 |
0.2 |
7.7 |
Indicated |
50 |
79.6 |
58.4 |
62.9 |
3.3 |
5.2 |
0.17 |
7.1 |
Inferred |
50 |
26.1 |
57.8 |
61.3 |
3.9 |
6.6 |
0.14 |
5.6 |
Total as at 30 June 2018 |
50 |
197.8 |
58.1 |
62.6 |
3.3 |
5.4 |
0.17 |
7.2 |
Total as at 30 June 2017 |
50 |
229.9 |
58.4 |
62.8 |
3.2 |
5.2 |
0.17 |
7.0 |
Source: BCI Minerals. Note: 100% BC Iron, subject to sale agreement with MIN.
Exhibit 5: Iron Valley ore reserve estimate
Classification |
Cut-off (% Fe) |
Mt |
Fe (%) |
Ca Fe (%) |
AI2O2 (%) |
SiO2 (%) |
P (%) |
LOI (%) |
Stockpiles (Proven) |
54 |
5.2 |
56.1 |
60.1 |
3.7 |
8.3 |
0.14 |
6.6 |
Proven |
54 |
56.6 |
58.4 |
63.3 |
3.1 |
4.6 |
0.19 |
7.7 |
Probable |
54 |
33.6 |
58.6 |
63.1 |
3.2 |
5.0 |
0.16 |
7.2 |
Total as at 30 June 2018 |
54 |
95.4 |
58.4 |
63.1 |
3.1 |
5.0 |
0.18 |
7.4 |
Total as at 30 June 2017 |
54 |
113.0 |
58.7 |
63.3 |
3.0 |
4.8 |
0.18 |
7.3 |
Source: BCI Minerals. Note: 100% BC Iron, subject to sale agreement with MIN.
Until August 2014, Iron Valley was a part of IOH and had a mine gate sale arrangement with MIN whereby the latter bore the operating expenses and purchased Iron Valley product at prices linked to MIN’s realised sale price – an arrangement that BCI retained after its acquisition of IOH in October 2014 (albeit with minor amendments). Note that BCI retains ownership of the tenements and certain statutory obligations, including payment of government, state and third-party royalties. The arrangement with MIN effectively means that BCI receives a royalty-type income stream from Iron Valley. Sales and earnings figures attributable to BCI from Iron Valley since 2014 have been as follows:
Exhibit 6: Iron Valley production and sales
Iron Valley |
FY15 |
FY16 |
FY17 |
FY18 |
Production per year (wmt*, millons) |
2.83 |
6.5 |
8.0 |
6.1 |
Revenue from Iron Valley to BCI (A$m) |
18.8 |
39.9 |
63.5 |
33.0 |
EBITDA** from Iron Valley to BCI (A$m) |
4.1 |
10.2 |
16.0 |
7.9 |
Source: BCI Minerals. Note: *wmt denotes wet metric tonnes; **company calculated.
Until recently, BCI’s received royalty was based on MIN’s received price for Iron Valley iron ore, whereas its paid royalty to the State Government, in particular, was based on an indexed price – a mechanism that gave rise to apparent anomalies and subsequent adjustments to BCI’s net income from Iron Valley. To correct this income volatility, BCI management engaged with State Government in the June quarter of 2018 and negotiated an agreement to alter the calculation of its paid royalties from an indexed price to a received price basis – with the result that net income from Iron Valley to BCI in recent quarters appears much smoother than in previous quarters and to approach an A$1/t approximation relative to wet metric tonne production.
MIN is seeking to implement an enhanced logistics solution for Iron Valley known as the Pilbara Infrastructure Project, which comprises an innovative 330km lightweight, narrow gauge rail transport system connecting to automated port infrastructure at Port Hedland with fully autonomous c 120t payload shuttles. Once operational, potential gains would include lower operating expenses and doubled production rates to 15Mtpa, leading to a direct benefit to BCI in the form of a corresponding increase in royalty payments as well as an indirect benefit in the form of Iron Valley’s becoming a more economically efficient operation.
Once appropriate state approvals have been received, construction of the project is likely to take 18 months before the system becomes operational. Note that for the purposes of our sensitivities’ sections on pages 20–22, in which we consider the valuation implications of a doubling of the sales rate at Iron Valley, we assume that construction of the Pilbara Infrastructure Project would be complete at the end of FY20, that commissioning and ramp-up would occur in FY21 and that full capacity will be reached in FY22.